A single rod bearing for high-speed rotation
A high-speed rotation, single-rod technology, applied in the field of bearing lubrication, can solve the problems of being unable to get close to the bearing, affecting the service life of the bearing, and replenishing lubricant for the bearing, so as to avoid the risk of overheating, prolong the service life and reduce the rotation resistance.
- Summary
- Abstract
- Description
- Claims
- Application Information
AI Technical Summary
Problems solved by technology
Method used
Image
Examples
Embodiment 1
[0047] like Figure 1 to Figure 2 The shown single-rod bearing for high-speed rotation includes: a bearing rod 10, a bearing sleeve 20 and a bearing washer 30, the bearing rod 10 is axially provided with a rolling step shaft 11 and a fixed step shaft 12 in turn; the bearing sleeve 20 sets A plurality of needle rollers 40 are installed on the rolling step shaft 11, and are located in the annular gap between the bearing sleeve 20 and the bearing rod 10 and are evenly distributed along the circumferential direction. The two adjacent needle rollers 40 and the inner hole wall form an oil collecting cavity 50; The bearing washer 30 is sleeved on the fixed step shaft 12 and abuts on the limit interface between the rolling step shaft 11 and the fixed step shaft 12 ; wherein, the end of the rolling step shaft 11 is provided with a bearing spacer 30 to match The limiting flange 13 is used to limit the axial movement of the bearing sleeve 20. The oil inlet grooves 21 are provided on both...
Embodiment 2
[0059] The difference between this embodiment and the first embodiment is that the structure of the oil inlet groove 21 is different, and the other structures are the same, which will not be repeated here. In this embodiment, as Figure 4 As shown, the oil inlet groove 21 is arc-shaped and penetrates radially from the outer edge to the inner hole; the depth of the oil inlet groove 21 from the outer edge to the inner hole gradually becomes deeper.
[0060] Specifically, the depth of the groove bottom is changed on the basis of the circumferential inclination of the oil inlet groove 21, so that the inclination angle of the end facing the inner hole becomes larger, and the contact area between the lubricating oil and the needle roller 40 is increased, and the oil inlet groove 21 is uniformly distributed along the circumferential direction. 3. When the bearing sleeve 20 rotates in the same direction as the inclination direction of the oil inlet groove 21, the pressure of the outer ...
PUM
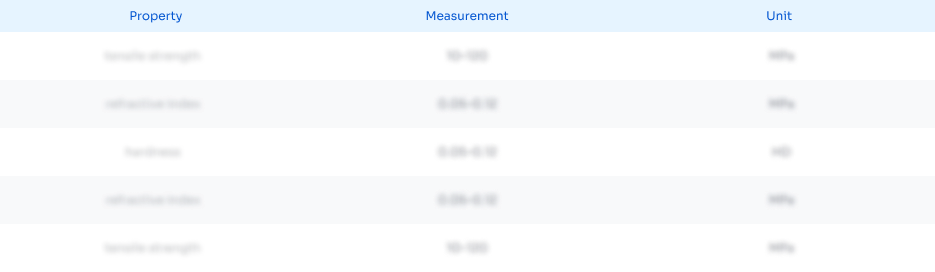
Abstract
Description
Claims
Application Information

- Generate Ideas
- Intellectual Property
- Life Sciences
- Materials
- Tech Scout
- Unparalleled Data Quality
- Higher Quality Content
- 60% Fewer Hallucinations
Browse by: Latest US Patents, China's latest patents, Technical Efficacy Thesaurus, Application Domain, Technology Topic, Popular Technical Reports.
© 2025 PatSnap. All rights reserved.Legal|Privacy policy|Modern Slavery Act Transparency Statement|Sitemap|About US| Contact US: help@patsnap.com