Thin ore body up-down medium-length hole subsequent filling mining method
A filling mining method and thin ore body technology, applied in underground mining, filling, surface mining, etc., can solve the problems of high blasting clamping, high labor intensity, low mining efficiency, etc., to reduce mining and cutting engineering, chiseling The effect of fast rock speed and high recovery efficiency
- Summary
- Abstract
- Description
- Claims
- Application Information
AI Technical Summary
Problems solved by technology
Method used
Image
Examples
Embodiment Construction
[0030] Such as figure 1 As shown, the thin ore body disclosed in this embodiment, the upper and lower middle and deep holes and subsequent filling mining method includes the following steps:
[0031] 1. Determine the structural parameters
[0032] The stope is arranged along the strike. According to the occurrence and dip angle of the ore body, determine the appropriate stope length. The width of the stope is the thickness of the ore body, and the height of the stope is the height of the middle section. The top and bottom columns are used to ensure the safe recovery of the lower middle section of the ore body.
[0033] 2. Construction mining and cutting engineering
[0034] In the middle section, the roadway along the vein at the bottom will be constructed horizontally along the ore body. An artificial false bottom is constructed at the bottom of the vein lane. In the upper and middle section along the ore body, the vein roadway is constructed, and the size of the vein roa...
PUM
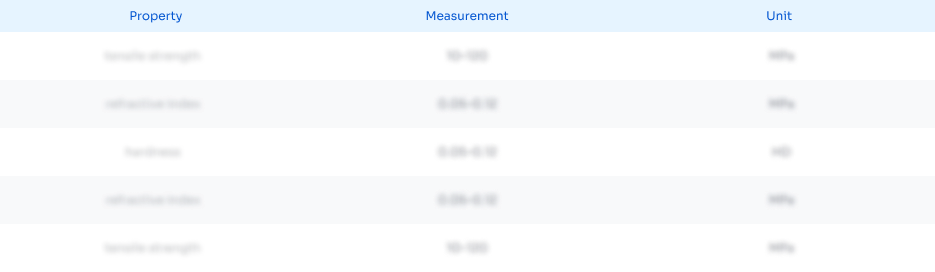
Abstract
Description
Claims
Application Information

- R&D
- Intellectual Property
- Life Sciences
- Materials
- Tech Scout
- Unparalleled Data Quality
- Higher Quality Content
- 60% Fewer Hallucinations
Browse by: Latest US Patents, China's latest patents, Technical Efficacy Thesaurus, Application Domain, Technology Topic, Popular Technical Reports.
© 2025 PatSnap. All rights reserved.Legal|Privacy policy|Modern Slavery Act Transparency Statement|Sitemap|About US| Contact US: help@patsnap.com