Composite cooling structure for turbine stator blade of gas turbine
A gas turbine and composite cooling technology, applied in mechanical equipment, engine components, machines/engines, etc., can solve problems such as poor temperature uniformity of blades, difficulties in mold design and manufacturing, and reduced service life of stationary blades, so as to improve overall temperature uniformity , Reduce manufacturing difficulty and cost, increase the effect of service life
- Summary
- Abstract
- Description
- Claims
- Application Information
AI Technical Summary
Problems solved by technology
Method used
Image
Examples
Embodiment 1
[0043] like Figure 1-6 As shown, the present invention provides a composite cooling structure for gas turbine stator blades, including a stator blade 1, the stator blade 1 is a hollow cooling blade, the upper end of the stator blade 1 has an upper edge plate 105, and the lower end has a lower edge plate 106. Multiple exhaust membrane holes 101 are set on the side wall; the first partition 107, the second partition 108 and the third partition 109 are arranged inside the stator blade 1, and the first partition 107 is formed between the front edge of the stator blade 1 and the first partition 107. A cavity 201, a second cavity 202 is formed between the first partition 107 and the second partition 108, a third cavity 203 is formed between the second partition 108 and the third partition 109, the third partition 109 A fourth inner cavity 204 is formed between the tail edge and the first inner cavity 201. A first blocking cover 7 is arranged below the first inner cavity 201, and a ...
Embodiment 2
[0054] Please refer to Figure 8 As shown, the difference between this embodiment and Embodiment 1 is that no protrusion is provided in the middle of the first partition 107, and four grooves are provided at both ends of the first partition 107, including two grooves in the first inner cavity 201. a groove, and two grooves in the second inner chamber 202, the cross section of the first ferrule 2 is U-shaped, and the two sides of the first ferrule 2 are inserted into the grooves on the first partition 107 for Positioning; the middle part of the second dividing plate 108 is not provided with protrusions, and the two ends of the second dividing plate 108 are provided with four grooves, including two grooves in the second inner cavity 202 and two grooves in the third inner cavity 203. two grooves, the second ferrule 3 is a straight sheet or a circular arc sheet with a certain radian, one end side of the two second ferrule 3 is inserted into the groove of the first partition 107, t...
PUM
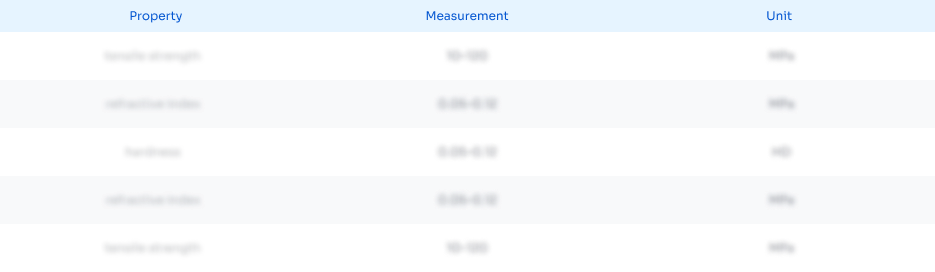
Abstract
Description
Claims
Application Information

- Generate Ideas
- Intellectual Property
- Life Sciences
- Materials
- Tech Scout
- Unparalleled Data Quality
- Higher Quality Content
- 60% Fewer Hallucinations
Browse by: Latest US Patents, China's latest patents, Technical Efficacy Thesaurus, Application Domain, Technology Topic, Popular Technical Reports.
© 2025 PatSnap. All rights reserved.Legal|Privacy policy|Modern Slavery Act Transparency Statement|Sitemap|About US| Contact US: help@patsnap.com