Clamping device with rotating mechanism
A technology of clamping device and rotating mechanism, applied in the direction of chuck, manipulator, transportation and packaging, etc., can solve the problems of low work efficiency, difficult to precisely control, single work, etc., to improve work efficiency and reliability, installation and maintenance. Convenient, wide-ranging effects
- Summary
- Abstract
- Description
- Claims
- Application Information
AI Technical Summary
Problems solved by technology
Method used
Image
Examples
Embodiment Construction
[0018] In order to make the purpose and technical solutions of the embodiments of the present invention more clear, the technical solutions of the embodiments of the present invention will be clearly and completely described below in conjunction with the drawings of the embodiments of the present invention. Wherein, in the description of the present invention, it should be noted that the orientations or positional relationships indicated by the terms "inner", "outer", "upper", "lower", "front", "rear" etc. are based on the drawings. The positional relationship shown is only for the convenience of describing the present invention and simplifying the description, but does not indicate or imply that the referred device or component must have a specific orientation, be constructed and operated in a specific orientation, and therefore cannot be construed as a limitation of the present invention. Based on the described embodiments of the present invention, all other embodiments obtai...
PUM
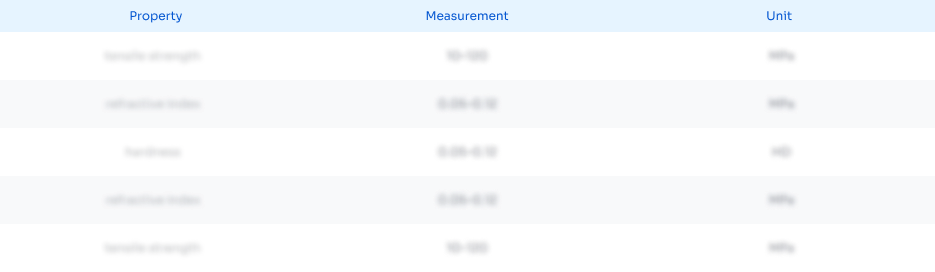
Abstract
Description
Claims
Application Information

- R&D
- Intellectual Property
- Life Sciences
- Materials
- Tech Scout
- Unparalleled Data Quality
- Higher Quality Content
- 60% Fewer Hallucinations
Browse by: Latest US Patents, China's latest patents, Technical Efficacy Thesaurus, Application Domain, Technology Topic, Popular Technical Reports.
© 2025 PatSnap. All rights reserved.Legal|Privacy policy|Modern Slavery Act Transparency Statement|Sitemap|About US| Contact US: help@patsnap.com