Laminated solid wood board and preparation process thereof
A preparation process, a technology of solid wood panels, applied in the direction of manufacturing tools, wood processing equipment, wood compression, etc., can solve the problems of solid wood panel mechanical strength, loss of insulation performance, easy peeling off of the structural layer, large internal stress, etc., to improve the quality of the board The effect of product quality, compensating for the loss of mechanical strength and eliminating residual stress
- Summary
- Abstract
- Description
- Claims
- Application Information
AI Technical Summary
Problems solved by technology
Method used
Examples
preparation example Construction
[0051] A kind of preparation technology of laminated solid wood board provided by the invention, it comprises the following steps:
[0052] Step 1, after completing one-step polishing treatment on the log plate, carbonization treatment is carried out to obtain plate A;
[0053] Step 2, after finishing the impregnation and curing treatment on the plate A, perform two-step polishing treatment to obtain the plate B;
[0054] Step 3, after the plate B is coated with an insulating layer, a step of hot-pressing treatment is performed to obtain the plate C;
[0055] Step 4, after coating the board C with a waterproof layer, performing two-step hot-pressing treatment to obtain the board D;
[0056] Step 5, after attaching the veneer according to the wood grain direction of the board D, a step of cold pressing is performed to obtain the board E;
[0057] Step 6: After the board E is painted and printed, two steps of cold pressing and three steps of polishing are performed to obtain a...
Embodiment 1
[0095] This embodiment discloses a preparation process of a laminated solid wood board. The process is used to prepare a laminated solid wood board. The process includes the following steps:
[0096] In step 1-a, the log plate is subjected to a rough grinding and polishing and a fine grinding and polishing in sequence; wherein, the rough grinding time is 100min, the rough grinding pressure is 5bar, the rough grinding temperature is 35°C, and the mesh size of the sandpaper used for rough grinding is 300 mesh; the fine grinding time is 100min, the fine grinding pressure is 5bar, the fine grinding temperature is 35°C, and the fine grinding sandpaper mesh is 1500 mesh;
[0097] Step 1-b, preheating process: spray heat-resistant resin on the board, and keep it warm at 60°C for 14 hours; wherein, the spraying conditions are: the spraying speed is 100mL / min, and the spraying amount is 200mL / m 2 ;
[0098] Low-temperature drying process: stop spraying the heat-resistant resin, move t...
Embodiment 2
[0112] This embodiment discloses a preparation process of a laminated solid wood board. The process is used to prepare a laminated solid wood board. The process includes the following steps:
[0113] In step 1-a, the log board is subjected to a rough grinding and polishing and a fine grinding and polishing in sequence; wherein, the rough grinding time is 120min, the rough grinding pressure is 5bar, the rough grinding temperature is 35°C, and the mesh size of the sandpaper used for rough grinding is 200 mesh; the fine grinding time is 100min, the fine grinding pressure is 5bar, the fine grinding temperature is 35°C, and the fine grinding sandpaper mesh is 1000 mesh;
[0114] Step 1-b, preheating process: spray heat-resistant resin on the board, and keep it warm at 80°C for 18 hours; wherein, the spraying conditions are: the spraying speed is 150mL / min, and the spraying amount is 300mL / m 2 ;
[0115] Low-temperature drying process: stop spraying the heat-resistant resin, move t...
PUM
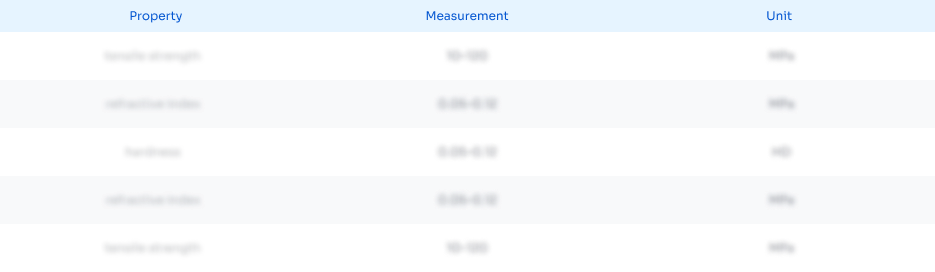
Abstract
Description
Claims
Application Information

- R&D
- Intellectual Property
- Life Sciences
- Materials
- Tech Scout
- Unparalleled Data Quality
- Higher Quality Content
- 60% Fewer Hallucinations
Browse by: Latest US Patents, China's latest patents, Technical Efficacy Thesaurus, Application Domain, Technology Topic, Popular Technical Reports.
© 2025 PatSnap. All rights reserved.Legal|Privacy policy|Modern Slavery Act Transparency Statement|Sitemap|About US| Contact US: help@patsnap.com