Reinforced sintering method for upper material layer
A technology of strengthening sintering and material layer, which is applied in the field of iron ore sintering in the metallurgical industry, can solve the problem of uneven heat distribution, achieve balanced heat distribution, prolong retention time, improve sintering capacity and sinter quality
- Summary
- Abstract
- Description
- Claims
- Application Information
AI Technical Summary
Problems solved by technology
Method used
Image
Examples
Embodiment 1
[0030] A method for strengthening the sintering of the upper material layer in this embodiment includes the following steps:
[0031] S1. Mixing of main ingredients: mix ore, flux and fuel, miscellaneous materials, blast furnace return ore, and internal return ore for batching, and the prepared materials are uniformly mixed once and granulated twice to obtain the secondary mixture for sintering; The main ingredient mixing process can be specifically determined according to practical requirements, and is a well-known conventional technology in the industry, and will not be described in detail;
[0032] S2. Mixing of auxiliary ingredients: batching of magnetic concentrate, flux and fuel, and mixing the prepared materials to obtain the primary mixture of sintering upper layer; the mixing process of auxiliary ingredients is determined according to actual needs, and is a well-known conventional technology in the industry ,No longer;
[0033] S3. Tertiary mixing: add the sintered u...
Embodiment 2
[0044] A kind of upper material layer strengthened sintering method of this embodiment is basically the same as embodiment 1, the difference is that in this embodiment, the height of the sintered secondary mixture layer is 75% of the total sintered layer thickness, and the sintered tertiary mixture layer height is 25% of the total layer thickness is sintered. More specifically, in this embodiment, only within the first third of the length of the sintering machine, the opening of the damper is gradually increased along the forward direction of the trolley, and the negative pressure of the draft is adjusted to gradually decrease to the negative pressure of sintering. Two-stage pressure regulation, the negative pressure adjustment scheme is shown in Table 1 below, and the sintering effect after implementation is shown in Table 2 below:
[0045] Table 1 Sintering ventilation negative pressure adjustment scheme
[0046]
[0047] Table 2 Sintering technology and quality indicato...
Embodiment 3
[0051] A kind of upper material layer strengthening sintering method of this embodiment is basically the same as embodiment 1, the difference is that in this embodiment, the height of the sintered secondary mixture layer is 50% of the sintered total layer thickness, and the sintered tertiary mixture layer height is Sinter 50% of the total layer thickness. More specifically, in this embodiment, the fuel content in the sintered secondary mixture is controlled to be 0.6% lower than the fuel content in the sintered monolithic mixture; the fuel content in the sintered tertiary mixture is 0.6% higher than the fuel content in the sintered monolithic mixture; Or: the alkalinity of the sintered secondary mixture is 0.3 lower than that of the sintered overall mixture; the alkalinity of the sintered tertiary mixture is 0.3 higher than that of the sintered overall mixture; or: the ratio of the magnetic concentrate in the sintered secondary mixture is sintered The overall magnetic concentr...
PUM
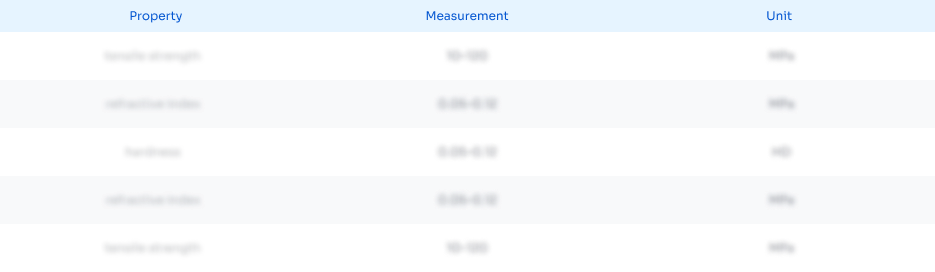
Abstract
Description
Claims
Application Information

- R&D Engineer
- R&D Manager
- IP Professional
- Industry Leading Data Capabilities
- Powerful AI technology
- Patent DNA Extraction
Browse by: Latest US Patents, China's latest patents, Technical Efficacy Thesaurus, Application Domain, Technology Topic, Popular Technical Reports.
© 2024 PatSnap. All rights reserved.Legal|Privacy policy|Modern Slavery Act Transparency Statement|Sitemap|About US| Contact US: help@patsnap.com