Nondestructive testing method for adapting to suspension arm through automatic telescopic obstacle avoidance
An automatic telescopic and non-destructive testing technology, applied in the direction of cranes, material magnetic variables, etc., can solve problems such as difficult detection and differences in the cross-sectional size of the boom, so as to prevent fracture accidents, ensure integrity status, and prevent missed and false detections Effect
- Summary
- Abstract
- Description
- Claims
- Application Information
AI Technical Summary
Problems solved by technology
Method used
Image
Examples
Embodiment 1
[0031] Such as figure 2 As shown, the cross-sectional shape of the boom 1 of the existing mobile crane is mostly U-shaped, that is, the upper surface and two sides of the boom 1 are planes, and the lower surface is approximately an arc surface.
[0032] Embodiment 1 of the present invention discloses a non-destructive testing method for adapting a boom through automatic telescopic obstacle avoidance, which is used for testing the boom 1 with the above cross-sectional shape. Such as Figure 2-11 As shown, the vehicle-mounted surface defect detection device includes: a mobile vehicle 2, a square main frame installed on the mobile vehicle 2, and a top inspection assembly, two side inspection assemblies and a bottom inspection assembly installed on the main frame. The main body frame is formed by connecting the top plate 3, one side plate 4, bottom plate 5 and the other side plate 4 sequentially from end to end, specifically, it can be connected by screws. Each detection assemb...
Embodiment 2
[0044]Embodiment 2 of the present invention discloses a non-destructive testing method for adapting a boom through automatic telescopic obstacle avoidance, which is the same as the method in Embodiment 1. Such as Figure 2-11 As shown, the vehicle-mounted surface defect detection device of the second embodiment is the same as that of the first embodiment. In addition, Embodiment 2 also specifically discloses an implementation structure of the top detection component, specifically as follows:
[0045] The number of the first detection parts is two. Each first detecting element includes: a first magnetic sensor array 9 . Each first magnetic sensitive sensor array 9 is arranged in each first sensor box 10, such as Figure 7 It is shown that it has a raised space for accommodating, and specifically, it can be sealed in the first sensor box 10 by epoxy resin. First magnets 11 are respectively arranged in the grooves at the front and rear ends of each first sensor box 10 , which...
Embodiment 3
[0054] Embodiment 3 of the present invention discloses a non-destructive testing method for adapting a boom through automatic telescopic obstacle avoidance, which is the same as the method in Embodiment 1 or 2. Such as Figure 2-11 As shown, the vehicle-mounted surface defect detection device of Embodiment 3 is the same as that of Embodiment 1 or 2. In addition, Embodiment 3 specifically discloses an implementation structure of the side detection component.
[0055] The second detection part includes: a second magnetic sensor array 24 . The second magnetic sensitive sensor array 24 is arranged in the second sensor box 25 , and specifically can be sealed in the second sensor box 25 by epoxy resin. The first sensor box 10 is generally located between the second sensor boxes 25 on both sides. Second magnets 26 are respectively arranged in the grooves at the front and rear ends of the second sensor box 25 , and can be specifically sealed in the second sensor box 25 by epoxy res...
PUM
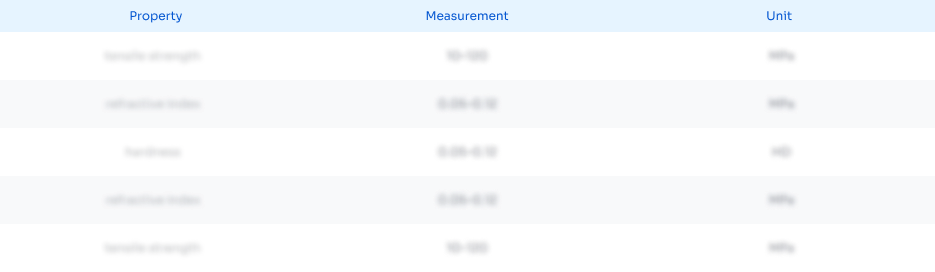
Abstract
Description
Claims
Application Information

- R&D Engineer
- R&D Manager
- IP Professional
- Industry Leading Data Capabilities
- Powerful AI technology
- Patent DNA Extraction
Browse by: Latest US Patents, China's latest patents, Technical Efficacy Thesaurus, Application Domain, Technology Topic, Popular Technical Reports.
© 2024 PatSnap. All rights reserved.Legal|Privacy policy|Modern Slavery Act Transparency Statement|Sitemap|About US| Contact US: help@patsnap.com