Industrial robot collision detection method
An industrial robot and collision detection technology, which is applied in the direction of manipulators, manufacturing tools, etc., can solve the problems of insufficient control compliance and inability to adjust
- Summary
- Abstract
- Description
- Claims
- Application Information
AI Technical Summary
Problems solved by technology
Method used
Image
Examples
Embodiment Construction
[0030] The present invention will be further described below.
[0031] A collision detection method for an industrial robot, characterized in that it includes collision detection based on a fixed threshold, collision detection combined with frequency domain analysis, robot response action design, robot collision detection experiment,
[0032] The collision detection based on the fixed threshold needs to establish a dynamic relation when the robot is not affected by external forces: When the robot is subjected to external force during operation, the dynamic relation becomes: The control method based on the collision detection of the fixed threshold makes the joints of the robot move according to the trapezoidal speed planning in the experiment, and calculates the theoretical torque and actual torque of the robot according to the steps of the control method, and records the joints in the case of no collision. Execute the theoretical torque and the actual torque collected in t...
PUM
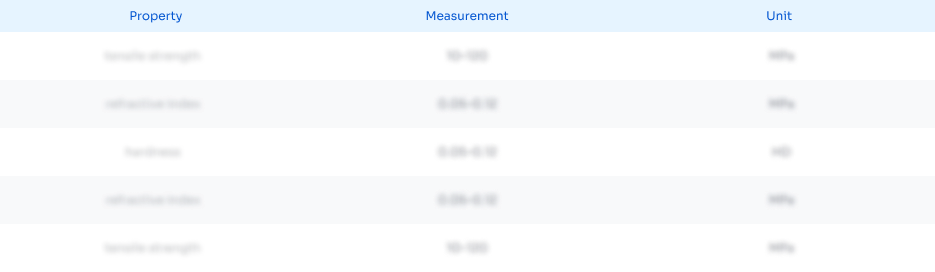
Abstract
Description
Claims
Application Information

- Generate Ideas
- Intellectual Property
- Life Sciences
- Materials
- Tech Scout
- Unparalleled Data Quality
- Higher Quality Content
- 60% Fewer Hallucinations
Browse by: Latest US Patents, China's latest patents, Technical Efficacy Thesaurus, Application Domain, Technology Topic, Popular Technical Reports.
© 2025 PatSnap. All rights reserved.Legal|Privacy policy|Modern Slavery Act Transparency Statement|Sitemap|About US| Contact US: help@patsnap.com