Multi-station injection molding mold
An injection molding, multi-station technology, applied in the field of molds, can solve problems such as easy-to-bond residual materials, white spots, and affect production efficiency, and achieve the effects of increasing the force-bearing area of ejection, reducing the number of uses, and increasing production efficiency.
- Summary
- Abstract
- Description
- Claims
- Application Information
AI Technical Summary
Problems solved by technology
Method used
Image
Examples
Embodiment Construction
[0025] In order to make the technical means, creative features, goals and effects achieved by the present invention easy to understand, the present invention will be further described below in conjunction with specific embodiments.
[0026] Such as Figure 1-Figure 9 As shown, a multi-station injection molding mold according to the present invention includes an upper mold clamping unit 1 and a lower mold clamping unit 2, the upper mold clamping unit 1 is located directly above the lower mold clamping unit 2, and the upper mold clamping unit 1 Cooperating with the lower mold clamping unit 2, the lower mold clamping unit 2 is provided with a plurality of ejector mechanisms 3, and the ejector rod mechanism 3 is provided with four circularly distributed cleaning mechanisms 4, and the lower mold clamping unit 2 is provided with a buffer Mechanism 5, an auxiliary mechanism 6 is provided between the upper mold clamping unit 1 and the lower mold clamping unit 2, through mutual mold cl...
PUM
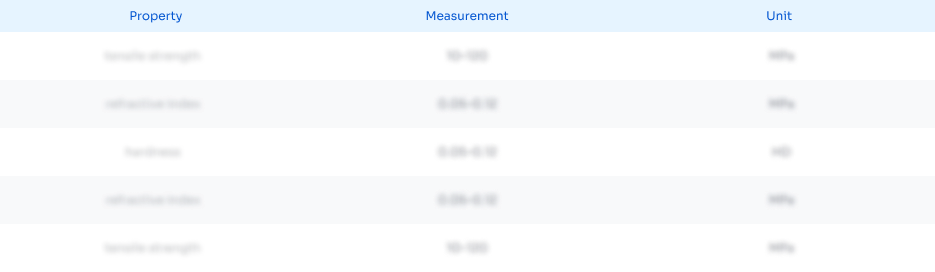
Abstract
Description
Claims
Application Information

- Generate Ideas
- Intellectual Property
- Life Sciences
- Materials
- Tech Scout
- Unparalleled Data Quality
- Higher Quality Content
- 60% Fewer Hallucinations
Browse by: Latest US Patents, China's latest patents, Technical Efficacy Thesaurus, Application Domain, Technology Topic, Popular Technical Reports.
© 2025 PatSnap. All rights reserved.Legal|Privacy policy|Modern Slavery Act Transparency Statement|Sitemap|About US| Contact US: help@patsnap.com