Multi-axis coupling hysteresis prediction method for piezoelectric actuator of atomic force microscope
An atomic force microscope and piezoelectric driver technology, applied in the field of precision manufacturing, can solve problems such as difficult multi-axis coupling hysteresis accurate measurement, and achieve the effect of improving high-speed and high-precision imaging, having versatility, and reducing computational complexity
- Summary
- Abstract
- Description
- Claims
- Application Information
AI Technical Summary
Problems solved by technology
Method used
Image
Examples
Embodiment Construction
[0034] In order to make the object, technical solution and advantages of the present invention clearer, the present invention will be further described in detail below in conjunction with the accompanying drawings and embodiments. It should be understood that the specific embodiments described here are only used to explain the present invention, not to limit the present invention. In addition, the technical features involved in the various embodiments of the present invention described below can be combined with each other as long as they do not constitute a conflict with each other.
[0035] An embodiment of the present invention provides a multi-axis coupling hysteresis prediction method for an atomic force microscope piezoelectric driver, such as figure 1 shown, including:
[0036] S1, inputting a periodic voltage signal to one axis of the piezoelectric driver to collect the displacement of the other axis;
[0037] S2, converting the displacement of the other axis into an...
PUM
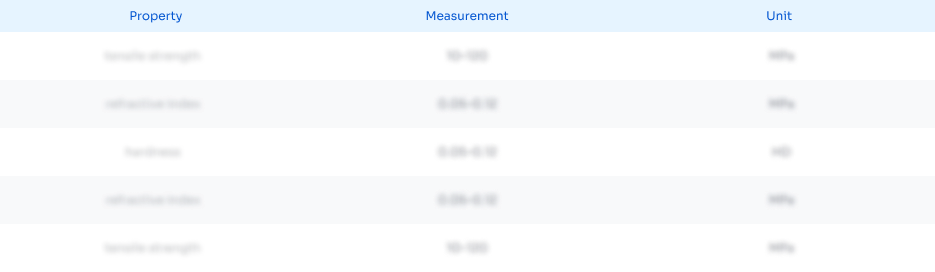
Abstract
Description
Claims
Application Information

- R&D
- Intellectual Property
- Life Sciences
- Materials
- Tech Scout
- Unparalleled Data Quality
- Higher Quality Content
- 60% Fewer Hallucinations
Browse by: Latest US Patents, China's latest patents, Technical Efficacy Thesaurus, Application Domain, Technology Topic, Popular Technical Reports.
© 2025 PatSnap. All rights reserved.Legal|Privacy policy|Modern Slavery Act Transparency Statement|Sitemap|About US| Contact US: help@patsnap.com