Magnetic control flexible ultrasonic transduction device
A technology of ultrasonic transduction and ultrasonic transducer, which is applied in the fields of ultrasonic detection, ultrasonic therapy, and ultrasonic imaging. It can solve the problems of physical damage to surface contact tissues, etc., and achieve the effects of small size, solving application difficulties, and controllable costs.
- Summary
- Abstract
- Description
- Claims
- Application Information
AI Technical Summary
Problems solved by technology
Method used
Image
Examples
Embodiment 2
[0082] Embodiment 2 of the present invention adds a magnetic flux gathering structure 1201 on the basis of Embodiment 1, including a magnetically permeable layer flexible support 12012 and a high-permeability magnetically permeable layer 12011 . Among them, the flexible support 12012 material of the magnetic conductive layer is Eco-flex-0030 with low Young's modulus, and the thickness of the spin coating is less than 30 μm, preferably 10-30 μm, and 10 μm is selected in this case. The high permeability magnetic layer 12011 is made of a composite material coated with high magnetic permeability soft magnetic material particles; the coating matrix material can be flexible Eco-flex-0030; the high magnetic permeability soft magnetic material particles are made of slope Molybdenum alloy, FeSi alloy, FeCoSiB, FeCrAlSi, FeSiBC, FeSiCrNi, etc.; thickness < 20μm, choose 20μm in case 2. Further, the magnetic flux gathering structure 1201 is arranged on the side of the upper half of the ma...
PUM
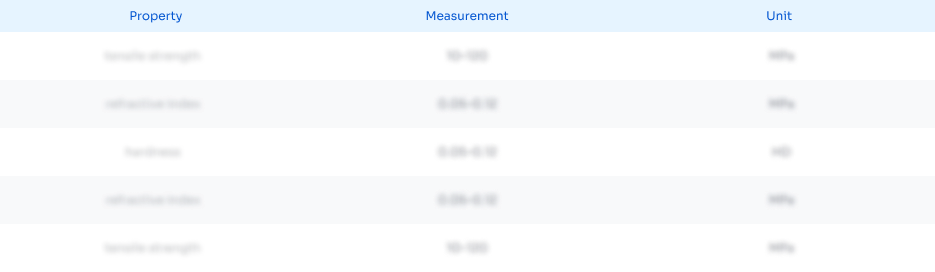
Abstract
Description
Claims
Application Information

- R&D
- Intellectual Property
- Life Sciences
- Materials
- Tech Scout
- Unparalleled Data Quality
- Higher Quality Content
- 60% Fewer Hallucinations
Browse by: Latest US Patents, China's latest patents, Technical Efficacy Thesaurus, Application Domain, Technology Topic, Popular Technical Reports.
© 2025 PatSnap. All rights reserved.Legal|Privacy policy|Modern Slavery Act Transparency Statement|Sitemap|About US| Contact US: help@patsnap.com