Station structure model correction analysis method and system
A technology of structural models and analysis methods, applied in the field of finite element analysis, can solve problems such as non-unique models, inability to meet engineering needs, lack of high-order modes, etc., to achieve the effect of improving the accuracy of data analysis
- Summary
- Abstract
- Description
- Claims
- Application Information
AI Technical Summary
Problems solved by technology
Method used
Image
Examples
Embodiment Construction
[0033] The specific implementation manners of the present invention will be further described in detail below in conjunction with the accompanying drawings and embodiments. The following examples are used to illustrate the present invention, but are not intended to limit the scope of the present invention.
[0034] figure 1 A flow chart of a station structure model correction analysis method provided by the present invention, such as figure 1 As shown, the methods include:
[0035] S1, establishing a finite element model for the station structure, specifying the units of interest in the finite element model as design variables;
[0036] S2, select the unit of interest from each part, and treat the unit with the same material as a super unit, each super unit contributes a design variable, and the material property of each design variable is assigned an elastic modulus;
[0037] S3, performing a sensitivity analysis on each of the superunits to obtain a Spearman rank correlat...
PUM
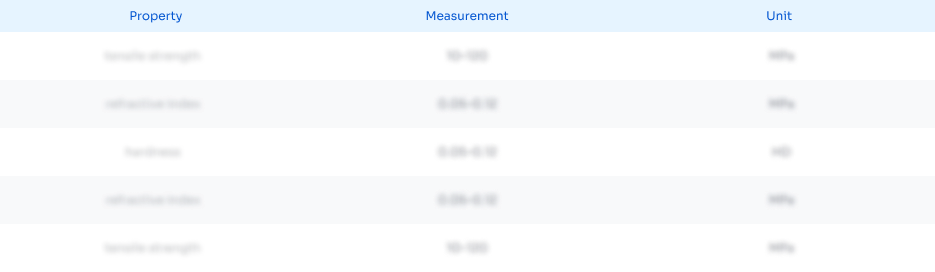
Abstract
Description
Claims
Application Information

- R&D
- Intellectual Property
- Life Sciences
- Materials
- Tech Scout
- Unparalleled Data Quality
- Higher Quality Content
- 60% Fewer Hallucinations
Browse by: Latest US Patents, China's latest patents, Technical Efficacy Thesaurus, Application Domain, Technology Topic, Popular Technical Reports.
© 2025 PatSnap. All rights reserved.Legal|Privacy policy|Modern Slavery Act Transparency Statement|Sitemap|About US| Contact US: help@patsnap.com