Conductive rubber for flexible sensor and preparation method thereof
A flexible sensor and conductive rubber technology, which is applied in the field of conductive rubber and its preparation, conductive rubber for flexible sensors and its preparation, can solve the problems of performance degradation and high resistance of conductive agent, and achieve the effect of improving conductive performance and perfecting conductive network
- Summary
- Abstract
- Description
- Claims
- Application Information
AI Technical Summary
Problems solved by technology
Method used
Image
Examples
specific Embodiment 1
[0033] The component raw materials are: 100 parts of natural latex (solid content 60wt.%); 3.0 parts of ordinary zinc oxide; 1.5 parts of accelerator ZDMC; 2.0 parts of sulfur; 3.0 parts of conductive carbon black SP; 10 parts of graphite KS6 ; Anti-aging agent 4010 is 1.0 parts; Sodium alginate is 1.0 parts.
[0034] Preparation method: weigh each component according to the amount of raw materials of the above components; add sodium alginate into water and stir for 15 minutes to fully dissolve, then add zinc oxide, accelerator ZDMC, sulfur, conductive carbon black SP, graphite KS6 and anti-aging After preliminary stirring and dispersing of agent 4010 into a slurry, the slurry was ground in a grinder at room temperature for 5 hours to form a stable and uniform aqueous dispersion of conductive agent; then the aqueous dispersion of conductive agent was added to natural rubber latex, and Stir at room temperature for 30 minutes to form a latex mixture; pour the latex mixture into ...
specific Embodiment 2
[0036] The component raw materials are: 100 parts of natural rubber latex (solid content 60wt.%); 5.0 parts of active zinc oxide; 2.0 parts of accelerator ZDMC; 3.0 parts of sulfur; 5.0 parts of conductive carbon black SP; 13 parts of graphite KS6 ; Antiaging agent 6PPD is 1.5 parts; Sodium polymethacrylate is 2.0 parts.
[0037] Preparation method: weigh each component according to the amount of raw materials of the above components; add sodium polymethacrylate into water and stir for 15 minutes to fully dissolve, then add active zinc oxide, accelerator ZDMC, sulfur, conductive carbon black SP, graphite KS6 After preliminarily stirring and dispersing into a slurry with the anti-aging agent 6PPD, the slurry was ground in a grinder at room temperature for 5 hours to form a stable and uniform aqueous dispersion of the conductive agent; then the aqueous dispersion of the conductive agent was added to the natural rubber latex and stirred at room temperature for 30 minutes to form ...
specific Embodiment 3
[0039]The component raw materials are: styrene-butadiene rubber emulsion (solid content 60wt.%) is 100 parts; active zinc oxide is 5.0 parts; accelerator ZDMC is 3.0 parts; sulfur is 2.0 parts; conductive carbon black SP is 5.0 parts; graphite KS6 is 15 parts; silver-plated nickel powder 5.0 parts; anti-aging agent DNP 2.0 parts; fatty alcohol polyoxyethylene ether sodium sulfate 5.0 parts.
[0040] Preparation method: weigh each component according to the amount of raw materials of the above components; add fatty alcohol polyoxyethylene ether sodium sulfate into water and stir for 15 minutes to fully dissolve, then add active zinc oxide, accelerator ZDMC, sulfur, conductive carbon black SP , graphite KS6, silver-plated nickel powder and anti-aging agent DNP are initially stirred and dispersed into a slurry, and the slurry is ground in a grinder at room temperature for 5 hours to form a stable and uniform aqueous dispersion of conductive agent; then the conductive Add the wate...
PUM
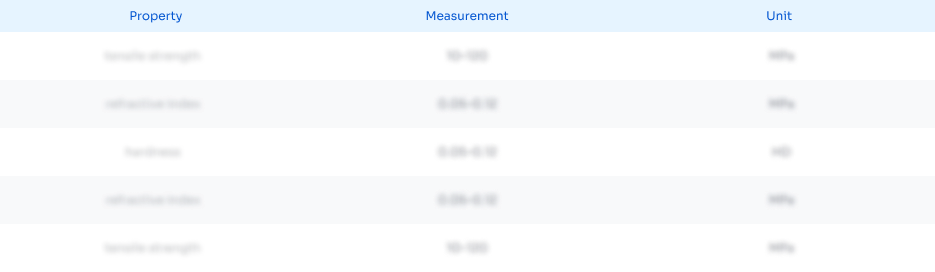
Abstract
Description
Claims
Application Information

- Generate Ideas
- Intellectual Property
- Life Sciences
- Materials
- Tech Scout
- Unparalleled Data Quality
- Higher Quality Content
- 60% Fewer Hallucinations
Browse by: Latest US Patents, China's latest patents, Technical Efficacy Thesaurus, Application Domain, Technology Topic, Popular Technical Reports.
© 2025 PatSnap. All rights reserved.Legal|Privacy policy|Modern Slavery Act Transparency Statement|Sitemap|About US| Contact US: help@patsnap.com