Weight reduction method for carbon fiber front fork or carbon fiber frame
A carbon fiber and frame technology, which is applied in the field of carbon fiber bicycle manufacturing, can solve the problems of heavy carbon fiber front fork 300, the left hook can not enter the air duct, and cannot meet the weight requirements of customers for lightweight products, so as to reduce the weight and overall The effect of weight and strength
- Summary
- Abstract
- Description
- Claims
- Application Information
AI Technical Summary
Problems solved by technology
Method used
Image
Examples
Embodiment Construction
[0024] The preferred embodiments of the present invention will be described below in conjunction with the accompanying drawings.
[0025] see Figure 2 to Figure 3d , the weight reduction method of the carbon fiber front fork of the first embodiment of the present invention comprises the following steps:
[0026] S001. Provide the one-piece front fork 100 formed by air pressure, see the status Figure 3a shown;
[0027] S002. Process the side draw through hole 30 at the position where the wishbone 10 of the integrated front fork 100 is close to the hook hole 20. For the status, see Figure 3b As shown; the air duct at the dropout 40 of the integrated front fork 100 is drawn away from the side pumping through hole 30; specifically, before the side pumping through hole 30 is processed on the wishbone 10, the A groove 60 is machined at the position of the hole 20, and then a side-drawing through hole 30 is machined on the groove bottom wall 61 of the groove 60, see Figure 3b...
PUM
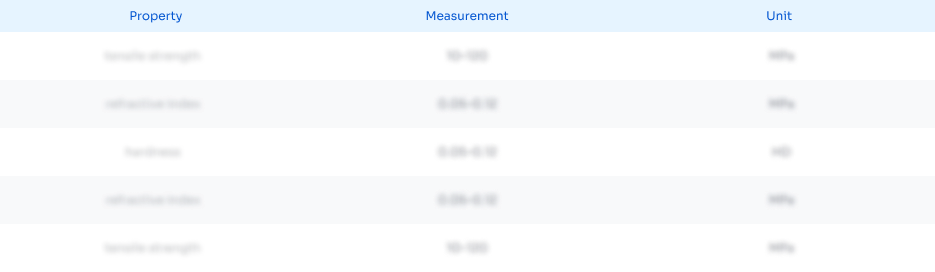
Abstract
Description
Claims
Application Information

- R&D
- Intellectual Property
- Life Sciences
- Materials
- Tech Scout
- Unparalleled Data Quality
- Higher Quality Content
- 60% Fewer Hallucinations
Browse by: Latest US Patents, China's latest patents, Technical Efficacy Thesaurus, Application Domain, Technology Topic, Popular Technical Reports.
© 2025 PatSnap. All rights reserved.Legal|Privacy policy|Modern Slavery Act Transparency Statement|Sitemap|About US| Contact US: help@patsnap.com