Preparation method of variable-rigidity wear-resistant vibration-damping composite material
A composite material and stiffness technology, which is used in the preparation of variable stiffness wear-resistant and vibration-damping composite materials, can solve the problems of cracking damage, peeling resistance, falling application, poor coating elongation, etc., so as to reduce the wear and tear of composite materials. Interlayer delamination failure behavior, easy operation, and the effect of improving the overall service life
- Summary
- Abstract
- Description
- Claims
- Application Information
AI Technical Summary
Problems solved by technology
Method used
Image
Examples
Embodiment 1
[0032] A variable stiffness wear-resistant and vibration-damping composite material is prepared, the length is 100mm±5mm, the width is 80mm±5mm, and the thickness is 2.4mm±0.2mm. The total number of layers is 3, and the steps are as follows:
[0033] (1) The composite material substrate with a thickness of 1.6mm ± 0.2mm was prepared by the T700 carbon fiber / epoxy plain fabric prepreg autoclave process.
[0034] (2) The composite material substrate is coated with 3340 type adhesive after surface treatment and cleaning.
[0035] (3) On the surface of one side of the substrate coated with the 3340 type adhesive composite material, along the movable friction side to the other side, the hydrogenated nitrile unvulcanized rubber with a thickness of 0.2mm ± 0.05mm is pasted, and its length, width and compound The material base is the same.
[0036](4) Continuously cover 0.3mm±0.1mm thick reinforced wear-resistant fabric from the surface width of 10mm on one side of the composite mat...
Embodiment 2
[0040] A variable stiffness wear-resistant and vibration-damping composite material is prepared, with a length of 500mm±5mm, a width of 120mm±5mm, and a thickness of 3mm±0.2mm. The total number of layers is 5, and the steps are as follows:
[0041] (1) A composite material substrate with a thickness of 2mm±0.2mm was prepared by a glass fiber / phenolic resin twill prepreg molding process.
[0042] (2) The composite material substrate is coated with 34T adhesive after surface treatment and cleaning.
[0043] (3) A silicone rubber unvulcanized rubber with a thickness of 0.2mm ± 0.05mm is pasted on the surface of one side of the substrate coated with the 34T type adhesive composite material along the movable friction side to the other side surface, and its length, width and composite material are The base material is the same.
[0044] (4) Continuously cover 0.2mm±0.1mm thick nylon 66 reinforced wear-resistant fabric from the surface width of 20mm on one side of the composite mat...
PUM
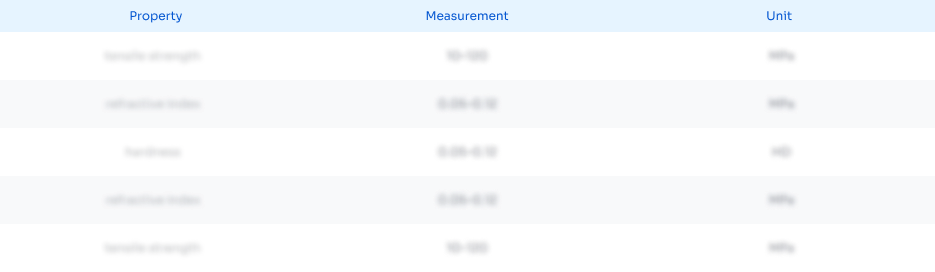
Abstract
Description
Claims
Application Information

- R&D
- Intellectual Property
- Life Sciences
- Materials
- Tech Scout
- Unparalleled Data Quality
- Higher Quality Content
- 60% Fewer Hallucinations
Browse by: Latest US Patents, China's latest patents, Technical Efficacy Thesaurus, Application Domain, Technology Topic, Popular Technical Reports.
© 2025 PatSnap. All rights reserved.Legal|Privacy policy|Modern Slavery Act Transparency Statement|Sitemap|About US| Contact US: help@patsnap.com