Self-adaptive mechanical claw based on Van der Waals force and friction force
A friction and self-adaptive technology, applied in the field of robotics, can solve the problems that pure adhesive materials cannot meet the grasping force, large grasping force, and cannot provide
- Summary
- Abstract
- Description
- Claims
- Application Information
AI Technical Summary
Problems solved by technology
Method used
Image
Examples
Embodiment Construction
[0025] The following will clearly and completely describe the technical solutions in the embodiments of the present invention with reference to the accompanying drawings in the embodiments of the present invention. Obviously, the described embodiments are only some, not all, embodiments of the present invention. Based on the embodiments of the present invention, all other embodiments obtained by persons of ordinary skill in the art without making creative efforts belong to the protection scope of the present invention.
[0026] See figure 1 , an adaptive mechanical gripper based on van der Waals force and friction, including a rotating base 1, two gripper bodies 2 connected to the swivel base 1, and a gripping end connected to one of the gripper bodies 2 The elastic component 3 and three dry adhesive components 4 connected to the clamping end of the other jaw main body 2, the clamping ends of the two clamping jaw main bodies 2 are parallel to each other, and the three dry adhe...
PUM
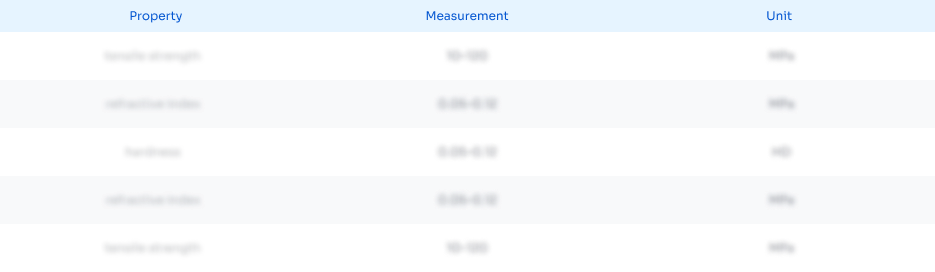
Abstract
Description
Claims
Application Information

- R&D
- Intellectual Property
- Life Sciences
- Materials
- Tech Scout
- Unparalleled Data Quality
- Higher Quality Content
- 60% Fewer Hallucinations
Browse by: Latest US Patents, China's latest patents, Technical Efficacy Thesaurus, Application Domain, Technology Topic, Popular Technical Reports.
© 2025 PatSnap. All rights reserved.Legal|Privacy policy|Modern Slavery Act Transparency Statement|Sitemap|About US| Contact US: help@patsnap.com