A 3D model nesting placement method based on model similarity
A similarity and model technology, applied in the field of 3D printing, can solve the problems of experience and time, complexity, poor effect, etc., to achieve the effect of low position, reduced support materials, and small occupied area
- Summary
- Abstract
- Description
- Claims
- Application Information
AI Technical Summary
Problems solved by technology
Method used
Image
Examples
Embodiment Construction
[0058] A nested arrangement method for 3D models based on model similarity, comprising the following steps:
[0059] Step 1: Take as figure 1 and figure 2 The 3D models S1 and S2 shown are taken as examples, and the surface of the bounding box of the 3D model is voxelized, such as image 3 and Figure 4 shown.
[0060] Step 2: The voxelized 3D models are combined and classified according to the similarity, and divided into similar model groups and non-similar models. The specific steps are as follows:
[0061] Step 2.1: The voxelized 3D model is bounded by the centerline of the bounding box, and the voxel projection is obtained: the projection of the lower half voxels on the xy plane, and the projection of the overall voxels on the xy plane.
[0062] Step 2.2: sort the 3D models according to the following order: the projected area of the 3D model in the xy direction, the voxel ratio, the number of voxels projected on the xy plane by the lower half of the voxels, and the...
PUM
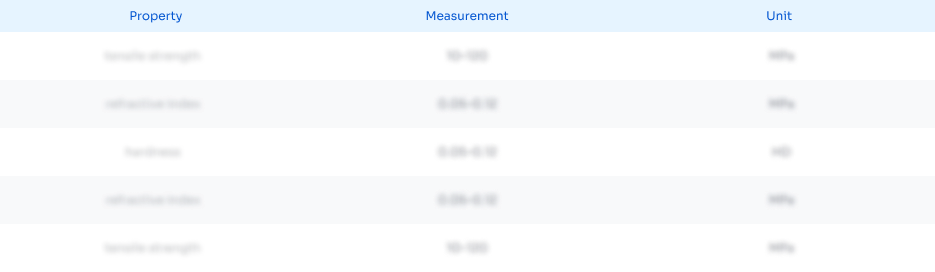
Abstract
Description
Claims
Application Information

- R&D
- Intellectual Property
- Life Sciences
- Materials
- Tech Scout
- Unparalleled Data Quality
- Higher Quality Content
- 60% Fewer Hallucinations
Browse by: Latest US Patents, China's latest patents, Technical Efficacy Thesaurus, Application Domain, Technology Topic, Popular Technical Reports.
© 2025 PatSnap. All rights reserved.Legal|Privacy policy|Modern Slavery Act Transparency Statement|Sitemap|About US| Contact US: help@patsnap.com