Porous and micropore combined throttling gas static pressure turning electric spindle
A gas static pressure, porous technology, applied in the direction of manufacturing tools, metal processing machinery parts, positioning devices, etc., can solve the problems of small bearing capacity, long pressurized gas flow, reduced rigidity of the static pressure spindle, etc., to improve the bearing capacity Effects of force and stiffness, reduced self-excited vibrations, reduced risk of clogging
- Summary
- Abstract
- Description
- Claims
- Application Information
AI Technical Summary
Problems solved by technology
Method used
Image
Examples
Embodiment
[0045] This embodiment combines the attached Figure 1-15 The porous and microporous combined throttling aerostatic turning electric spindle of the present invention will be described in detail.
[0046] The porous and microporous combined throttling gas static pressure turning electric spindle of the present invention includes an air bearing assembly 1 and a driving assembly 2, wherein figure 1 The left figure in the figure is a structural schematic diagram of the air bearing assembly 1, figure 1 The right figure in the figure is a structural schematic diagram of the drive assembly 2; the air bearing assembly 1 is composed of a base 101, a backing ring 102, a thrust plate 103, a debris plate 104, a suction cup 105, a filter plug 106, a rotating shaft 107, and two air blocking Composed of rod 108, 2 axial restrictors 109 and 2 radial restrictors 110, drive assembly 2 consists of stator mounting part 201, cooling sleeve 202, stator pressure plate 203, protective sleeve 204, gr...
PUM
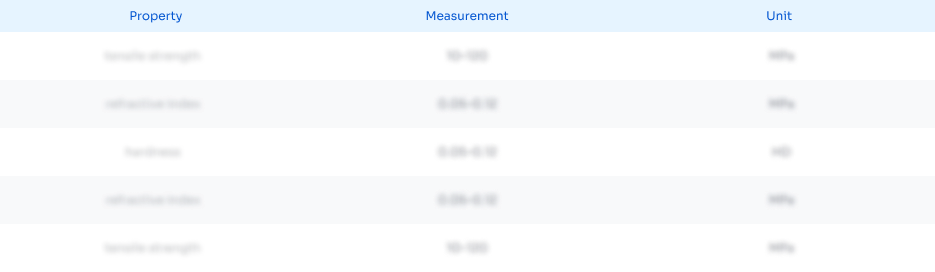
Abstract
Description
Claims
Application Information

- Generate Ideas
- Intellectual Property
- Life Sciences
- Materials
- Tech Scout
- Unparalleled Data Quality
- Higher Quality Content
- 60% Fewer Hallucinations
Browse by: Latest US Patents, China's latest patents, Technical Efficacy Thesaurus, Application Domain, Technology Topic, Popular Technical Reports.
© 2025 PatSnap. All rights reserved.Legal|Privacy policy|Modern Slavery Act Transparency Statement|Sitemap|About US| Contact US: help@patsnap.com