General assembly tray for improving loading efficiency of whole vehicle seat and method thereof
A technology for trays and seats is applied in the field of final assembly trays to improve the loading efficiency of vehicle seats, which can solve the problems of high assembly costs, seat guards, face covering indentations, scratches, etc., and achieves increased convenience. , to ensure the effect of integrity and aesthetics
- Summary
- Abstract
- Description
- Claims
- Application Information
AI Technical Summary
Problems solved by technology
Method used
Image
Examples
Embodiment 1
[0048] Embodiment 1: according to the appended figure 1 to attach Image 6 The shown assembly pallet improves the loading efficiency of the vehicle seat, which includes a pallet bottom plate 1, and one side of the pallet bottom plate 1 is rotatably installed with a rotatable first blocking pipe 2, which is close to the pallet bottom plate The other side of 1 is adapted to be rotatably installed with a yoke-type fourth baffle pipe 6, and the tray bottom plate 1 is adapted to be rotatably installed with a baffle pipe 6 between the first baffle pipe 2 and the fourth baffle pipe 6. The second blocking pipe 3, the third blocking pipe 4, the fifth blocking pipe 8, the sixth blocking pipe 7 is rotatably installed on the fifth blocking pipe 8;
[0049] The horizontal pipe directions of the first blocking pipe 2, the second blocking pipe 3, the third blocking pipe 4, the fourth blocking pipe 6 and the fifth blocking pipe 8 are in the same direction;
[0050] The first blocking pipe 2...
PUM
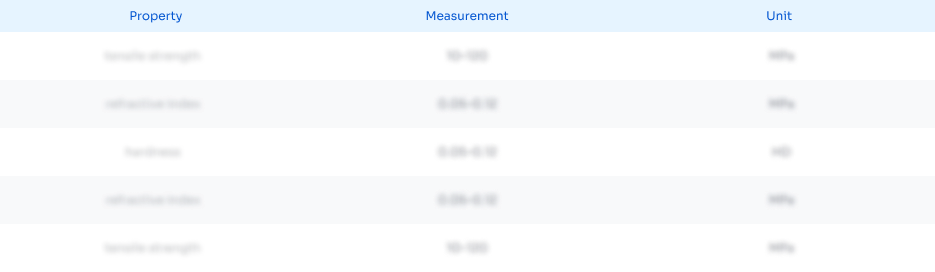
Abstract
Description
Claims
Application Information

- R&D Engineer
- R&D Manager
- IP Professional
- Industry Leading Data Capabilities
- Powerful AI technology
- Patent DNA Extraction
Browse by: Latest US Patents, China's latest patents, Technical Efficacy Thesaurus, Application Domain, Technology Topic, Popular Technical Reports.
© 2024 PatSnap. All rights reserved.Legal|Privacy policy|Modern Slavery Act Transparency Statement|Sitemap|About US| Contact US: help@patsnap.com