A Small Orifice Throttle Hydrostatic Thrust Gas Bearing with Accompanying Orifice
A gas bearing and orifice technology, applied in the direction of bearings, shafts and bearings, mechanical equipment, etc., can solve the problems of bearing micro-vibration, affecting the working stability of the system, affecting the working accuracy of the bearing, etc., to reduce micro-vibration, suppress Vortex development, the effect of improving work stability
- Summary
- Abstract
- Description
- Claims
- Application Information
AI Technical Summary
Problems solved by technology
Method used
Image
Examples
Embodiment Construction
[0030] figure 1 It is a schematic cross-sectional view of a small-hole throttling hydrostatic thrust gas bearing with an associated throttling hole according to an embodiment of the present application when it is in operation. figure 2 yes figure 1 A schematic cross-sectional view of an orifice throttle hydrostatic thrust gas bearing with an accompanying orifice is shown. image 3 yes figure 1 Schematic top view of an orifice throttle hydrostatic thrust gas bearing with accompanying orifice shown. Figure 4 yes image 3 Schematic enlargement of the pressure chamber and orifice shown in .
[0031] Such as figure 1 shown, see also Figure 2-Figure 4 , this embodiment provides a small-hole throttling static pressure thrust gas bearing with an accompanying orifice, which generally includes a bearing body 1, an air intake chamber 2, a main orifice 3, and an accompanying orifice 4 and pressure chamber 5. The bearing body 1 has a thrust surface. The air inlet chamber 2 is o...
PUM
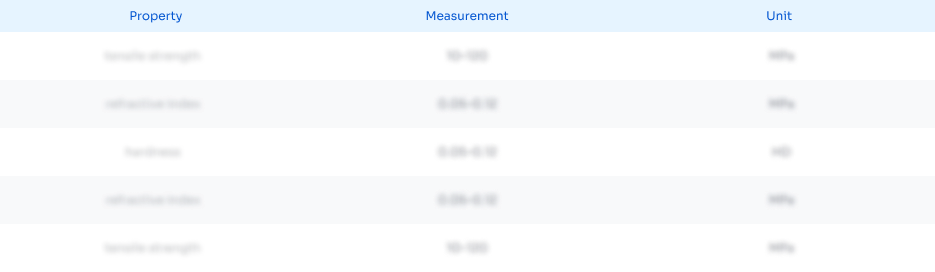
Abstract
Description
Claims
Application Information

- R&D
- Intellectual Property
- Life Sciences
- Materials
- Tech Scout
- Unparalleled Data Quality
- Higher Quality Content
- 60% Fewer Hallucinations
Browse by: Latest US Patents, China's latest patents, Technical Efficacy Thesaurus, Application Domain, Technology Topic, Popular Technical Reports.
© 2025 PatSnap. All rights reserved.Legal|Privacy policy|Modern Slavery Act Transparency Statement|Sitemap|About US| Contact US: help@patsnap.com