CSP manufacturing process
A manufacturing process and fluorescent film technology, which is applied to semiconductor devices, electrical components, circuits, etc., can solve problems such as difficulty in controlling the shape and dosage of fluorescent glue, difficulty in ensuring the quality of LEDs in chip-level packaging, and difficulty in controlling the uniformity of thickness of fluorescent glue. , to avoid deformation, avoid damage to electrodes, and achieve good stability
- Summary
- Abstract
- Description
- Claims
- Application Information
AI Technical Summary
Problems solved by technology
Method used
Image
Examples
Embodiment Construction
[0019] The present invention will be further described below in conjunction with the accompanying drawings of the description.
[0020] A CSP, including a fluorescent film support and a flip-chip LED chip 4 combined with a fluorescent film support 1, the fluorescent film support 1 includes a top light-emitting surface and four side light-emitting surfaces, and a crystal-bonding cavity 2 is formed in the fluorescent film support , the volume of the solid crystal cavity 2 is greater than the volume of the flip-chip LED chip 4, a gap is provided between the flip-chip LED chip 4 and the inner surface of the fluorescent film support 1 and is filled with glue, and the flip-chip LED chip 4 passes through the glue and the fluorescent film When the bracket 1 is combined, since the glue is transparent glue, and the gap between the flip-chip LED chip 4 and the fluorescent film bracket 1 is uniform, it is ensured that the overall light output of the CSP is uniform.
[0021] Such as figur...
PUM
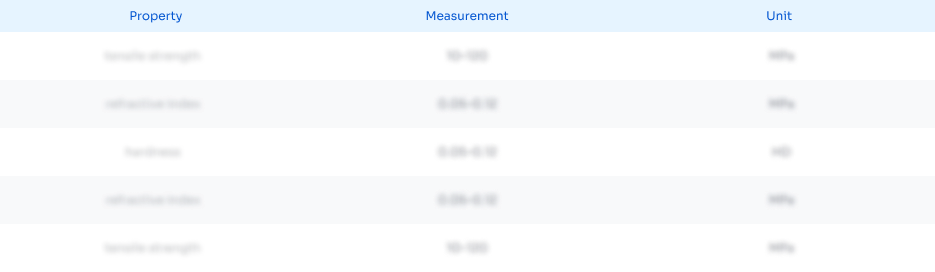
Abstract
Description
Claims
Application Information

- R&D
- Intellectual Property
- Life Sciences
- Materials
- Tech Scout
- Unparalleled Data Quality
- Higher Quality Content
- 60% Fewer Hallucinations
Browse by: Latest US Patents, China's latest patents, Technical Efficacy Thesaurus, Application Domain, Technology Topic, Popular Technical Reports.
© 2025 PatSnap. All rights reserved.Legal|Privacy policy|Modern Slavery Act Transparency Statement|Sitemap|About US| Contact US: help@patsnap.com