Hot melting equipment for PVC (polyvinyl chloride) pipe processing
A PVC pipe and hot-melt technology, applied in grain processing, etc., can solve the problems of not being able to control the feeding rate of hot-melt raw materials in real time, the position of feeding materials, and the reduction of hot-melt efficiency
- Summary
- Abstract
- Description
- Claims
- Application Information
AI Technical Summary
Problems solved by technology
Method used
Image
Examples
Embodiment 1
[0037] Such as figure 1 , a kind of hot-melt equipment for PVC pipe processing, including a fixed support plate 1, a hot-melt box 2 and a feed control mechanism 3, the feed control mechanism 3 is located directly above the hot-melt box 2, and the fixed support plate 1 It is fixedly connected to the upper end of the feed control mechanism 3, and four fixed support plates 1 are provided. By setting the feeding control mechanism 3 directly above the hot melting box 2, the raw material particles crushed to a specified size can be dropped into the inside of the hot melting box 2 for rapid hot melting treatment by using the feeding control mechanism 3. The material control mechanism 3 can control the position of the raw material particles falling in the hot melt box 2 and the discharge speed of the feed material, and can quickly make the four delivery ports in the feed control mechanism 3 close without feeding into the hot melt box 2. Feed body.
Embodiment 2
[0039] Such as figure 2 , as a further optimization scheme of the above embodiment: a hot-melt equipment for PVC pipe processing, including a fixed support plate 1, a hot-melt box 2 and a feed control mechanism 3, the feed control mechanism 3 is located at the bottom of the hot-melt box 2 Directly above, the fixed support plate 1 is fixedly connected to the upper end of the feed control mechanism 3, and there are four fixed support plates 1 . The feeding control mechanism 3 includes a material guiding device 4 and a closing control device 5 , and the closing control device 5 is fixedly installed inside the bottom end of the material guiding device 4 . Through the closing control device 5, the four feeding ports provided at the bottom of the material guide device 4 can be synchronously and quickly closed. Through the material guide device 4, the material body can be broken and the granular raw materials that meet the size will be discharged and transported. And the feeding de...
Embodiment 3
[0041] Such as image 3 , as a further optimization scheme of the above embodiment: a hot-melt equipment for PVC pipe processing, including a fixed support plate 1, a hot-melt box 2 and a feed control mechanism 3, the feed control mechanism 3 is located at the bottom of the hot-melt box 2 Directly above, the fixed support plate 1 is fixedly connected to the upper end of the feed control mechanism 3, and there are four fixed support plates 1 . The feeding control mechanism 3 includes a material guiding device 4 and a closing control device 5 , and the closing control device 5 is fixedly installed inside the bottom end of the material guiding device 4 . The material guide device 4 includes a material guide box 6, a baffle plate 7, a feed trough 8, an electro-hydraulic push rod 9, a fixed mounting frame 10, a feed box 11, a driving rod 12, a first motor 13, a stirring and crushing wheel 14 and delivery pipe 15, the first motor 13 is fixedly connected to the upper end of the driv...
PUM
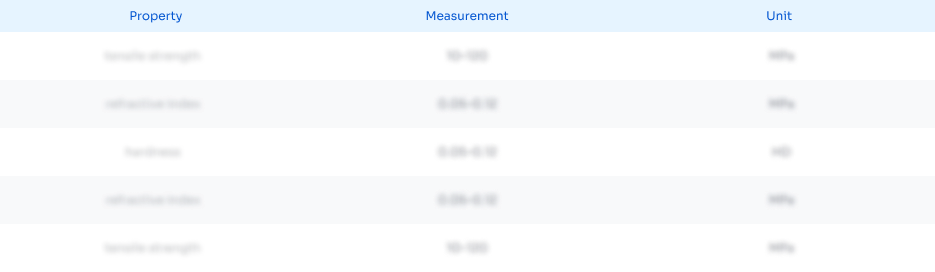
Abstract
Description
Claims
Application Information

- R&D Engineer
- R&D Manager
- IP Professional
- Industry Leading Data Capabilities
- Powerful AI technology
- Patent DNA Extraction
Browse by: Latest US Patents, China's latest patents, Technical Efficacy Thesaurus, Application Domain, Technology Topic, Popular Technical Reports.
© 2024 PatSnap. All rights reserved.Legal|Privacy policy|Modern Slavery Act Transparency Statement|Sitemap|About US| Contact US: help@patsnap.com