System and method for suppressing vibration of rotor in magnetic suspension bearing system
A technology of magnetic suspension bearing and rotor vibration, which is applied in magnetic bearing, restraining motor vibration control, bearing and other directions, which can solve the problems of error, inability to quickly reduce rotor impact and vibration, and inability of magnetic suspension bearing to provide active restraint force in time.
- Summary
- Abstract
- Description
- Claims
- Application Information
AI Technical Summary
Problems solved by technology
Method used
Image
Examples
Embodiment Construction
[0034] Such as Figure 5 As shown, a rotor vibration suppression system in a magnetic suspension bearing system includes: a magnetic suspension bearing system, a displacement sensor, a base acceleration feedforward compensator, a rotor disturbance compensation observer, a notch filter, a position controller, a power amplifier; a displacement The sensor is used to detect the rotor displacement; two differential circuits and a filter link are added to the conditioning circuit of the displacement sensor, and the rotor vibration displacement signal is differentiated twice to obtain the rotor vibration acceleration signal; the rotor disturbance compensation observer is used to receive the rotor vibration displacement signal, The rotor vibration acceleration signal, and send the rotor vibration suppression compensation control signal to the power amplifier; the power amplifier is used to adjust the control current of the magnetic suspension bearing; the base acceleration feedforward ...
PUM
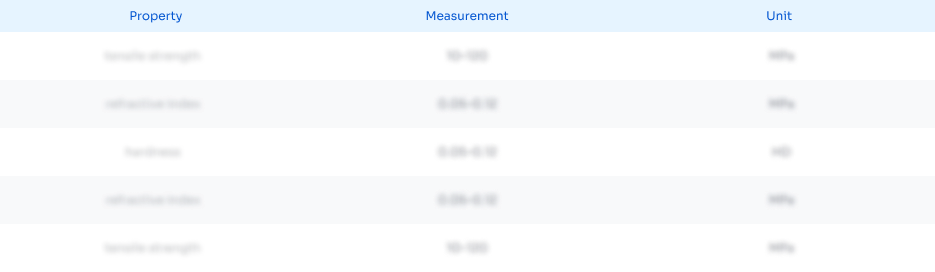
Abstract
Description
Claims
Application Information

- R&D Engineer
- R&D Manager
- IP Professional
- Industry Leading Data Capabilities
- Powerful AI technology
- Patent DNA Extraction
Browse by: Latest US Patents, China's latest patents, Technical Efficacy Thesaurus, Application Domain, Technology Topic, Popular Technical Reports.
© 2024 PatSnap. All rights reserved.Legal|Privacy policy|Modern Slavery Act Transparency Statement|Sitemap|About US| Contact US: help@patsnap.com