Rolling bearing three-dimensional dynamic rigidity testing device and testing method thereof
A technology of rolling bearings and test devices, which is applied in the direction of measuring devices, testing of mechanical components, testing of machine/structural components, etc. It can solve the problems affecting the test accuracy of bearing dynamic stiffness, integration, and ineffective simulation of dynamic radial and axial excitations, etc. question
- Summary
- Abstract
- Description
- Claims
- Application Information
AI Technical Summary
Problems solved by technology
Method used
Image
Examples
Embodiment Construction
[0040] The specific implementation manners of the present invention will be further described below in conjunction with the accompanying drawings and technical solutions.
[0041] It should be understood that the appended drawings are not to scale, presenting a suitably simplified representation of various features illustrative of the basic principles of the invention. The specific design features of the invention disclosed herein, including, for example, specific dimensions, orientations, locations and shapes will be determined in part by the particular intended application and use environment.
[0042] In the accompanying figures, the same or equivalent parts (elements) are designated with the same reference numerals.
[0043] In the description of the present invention, it should be noted that the terms "center", "longitudinal", "transverse", "upper", "lower", "front", "rear", "left", "right", " The orientations or positional relationships indicated by "vertical", "horizon...
PUM
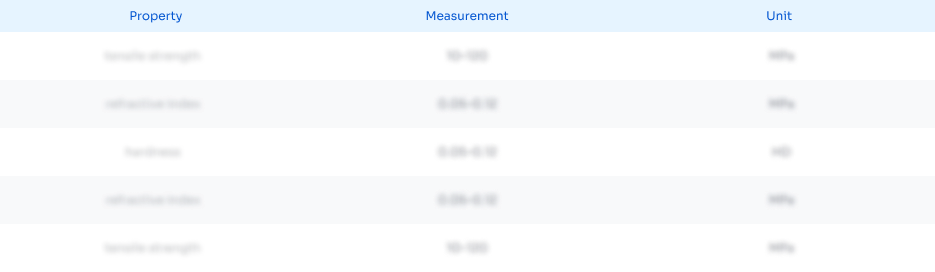
Abstract
Description
Claims
Application Information

- R&D
- Intellectual Property
- Life Sciences
- Materials
- Tech Scout
- Unparalleled Data Quality
- Higher Quality Content
- 60% Fewer Hallucinations
Browse by: Latest US Patents, China's latest patents, Technical Efficacy Thesaurus, Application Domain, Technology Topic, Popular Technical Reports.
© 2025 PatSnap. All rights reserved.Legal|Privacy policy|Modern Slavery Act Transparency Statement|Sitemap|About US| Contact US: help@patsnap.com