MMA continuous prepolymerization system and technology
A prepolymerization and process technology, applied in the MMA continuous prepolymerization system and its process field, can solve the problems of quality difference, unfavorable control reaction, extrusion time, inability to realize continuous polymerization extrusion molding, etc.
- Summary
- Abstract
- Description
- Claims
- Application Information
AI Technical Summary
Problems solved by technology
Method used
Image
Examples
Embodiment 1
[0034] MMA continuous pre-polymerization process steps are as follows:
[0035] a. Batching and feeding: Add MMA monomer, initiator and chain transfer agent with a weight ratio of 99:0.65:0.35 to each tank respectively, and each tank is injected into the reactor through the respective feed flow meters through the metering pump according to the proportion Inside, the extrusion injection flow rate of the reactor is 3kg / min, and the total amount is 80kg;
[0036] b. Reactor heating and stirring: set the temperature of the oil temperature machine to a value between 110°C, and heat the mixed fluid in the reactor at a constant temperature. When heating, the stirring blade of the reactor is turned on, and the rotation speed is 80r / min;
[0037] c. Torque calibration: for the first feed reaction, the flow meter at the bottom of the reactor sends out the polymerization solution several times, and the different viscosities of the polymerization solution are detected and the torque senso...
Embodiment 2
[0041] MMA continuous pre-polymerization process steps are as follows:
[0042] a. Batching and feeding: Add MMA monomer, initiator and chain transfer agent with a weight ratio of 99:0.65:0.35 to each tank respectively, and each tank is injected into the reactor through the respective feed flow meters through the metering pump according to the proportion Inside, the extrusion injection flow rate of the reactor is 4kg / min, and the total amount is 80kg;
[0043] b. Reactor heating and stirring: set the temperature of the oil temperature machine to a value between 100°C, and heat the mixed fluid in the reactor at a constant temperature. When heating, the stirring blade of the reactor is turned on, and the rotation speed is 70r / min;
[0044] c. Torque calibration: for the first feed reaction, the flow meter at the bottom of the reactor sends out the polymerization solution several times, and the different viscosities of the polymerization solution are detected and the torque senso...
Embodiment 3
[0048] MMA continuous pre-polymerization process steps are as follows:
[0049] a. Batching and feeding: Add MMA monomer, initiator and chain transfer agent with a weight ratio of 99:0.65:0.35 to each tank respectively, and each tank is injected into the reactor through the respective feed flow meters through the metering pump according to the proportion Inside, the extrusion injection flow rate of the reactor is 5kg / min, and the total amount is 80kg;
[0050] b. Reactor heating and stirring: set the temperature of the oil temperature machine to a value between 90°C, and heat the mixed fluid in the reactor at a constant temperature. When heating, the stirring blade of the reactor is turned on, and the rotation speed is 50r / min;
[0051] c. Torque calibration: for the first feed reaction, the flow meter at the bottom of the reactor sends out the polymerization solution several times, and the different viscosities of the polymerization solution are detected and the torque sensor...
PUM
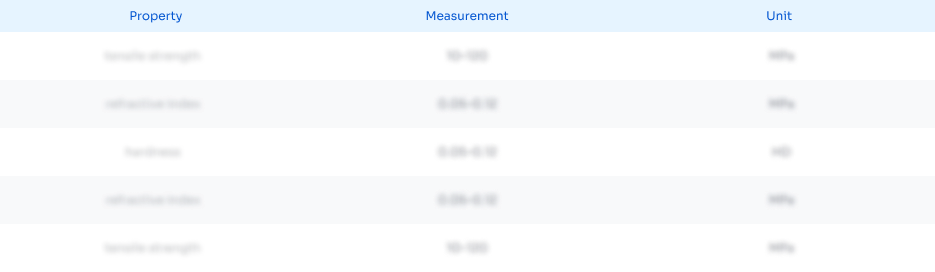
Abstract
Description
Claims
Application Information

- R&D Engineer
- R&D Manager
- IP Professional
- Industry Leading Data Capabilities
- Powerful AI technology
- Patent DNA Extraction
Browse by: Latest US Patents, China's latest patents, Technical Efficacy Thesaurus, Application Domain, Technology Topic, Popular Technical Reports.
© 2024 PatSnap. All rights reserved.Legal|Privacy policy|Modern Slavery Act Transparency Statement|Sitemap|About US| Contact US: help@patsnap.com