Pipe polishing and detecting integrated production line
A production line and pipe material technology, applied in the direction of grinding/polishing equipment, surface polishing machine tools, grinding/polishing safety devices, etc., can solve the problems of manpower consumption, low production efficiency, manual feeding, etc., to save manpower, Avoid the effect of manual handling
- Summary
- Abstract
- Description
- Claims
- Application Information
AI Technical Summary
Problems solved by technology
Method used
Image
Examples
Embodiment 1
[0039] see Figure 1-3 , an integrated production line for pipe polishing and detection, including an automatic feeding rack 11 for feeding pipe materials, a pipe polishing machine 12 is arranged behind the automatic feeding rack 11, and a pipe polishing machine 12 is arranged behind the pipe polishing machine 12 Polishing transition frame 13, the rear of the polishing transition frame 13 is provided with an eddy current flaw detection automatic detection device 14; the pipe is transported to the pipe polishing machine 12 through the automatic feeding frame 11 for automatic polishing, and after polishing is completed, it enters through the polishing transition frame 13 The eddy current flaw detection automatic detection device 14 performs detection, and classifies the detection as qualified or unqualified. The entire assembly line is fully automatic without manual operation, which is very convenient.
Embodiment 2
[0041] Embodiment 2 is a further description of Embodiment 1, and the same parts will not be repeated here, please refer to Figure 1-3 , the first rotating shaft 111 is arranged in the automatic feeding rack 11, the second rotating shaft 112 is arranged obliquely below the first rotating shaft 111, the sleeve 113 is arranged on the first rotating shaft 111, and the second rotating shaft 112 is arranged There is a winding wheel 1120; the automatic feeding rack 11 is also provided with a feeding belt 114, one side of the feeding belt 114 is connected with the automatic feeding rack 11, and the other side bypasses the sleeve 113 and the winding belt The wheel 1120 is connected; the rear of the sleeve 113 is provided with a leveling conveyor belt 115, and the end of the leveling conveyor belt 115 is provided with an inclined feeding slope 116, and the end of the feeding slope 116 is provided with a limit plate 117 A pusher cylinder 118 is arranged below the end of the feeding slo...
Embodiment 3
[0044] The third embodiment is a further description of the first embodiment, and the same parts will not be repeated here, please refer to Figure 1-3 A water tank 121 is arranged below the pipe polishing machine 12, and part of the water is poured into the water tank 121 to form an adsorption layer, which can filter the dust-entrained air entering the water tank 121; a casing 122 is set above the water tank 121, The whole polishing machine is sealed to play the role of preliminary noise reduction; the first partition 123 is installed above the water tank 121 and in the shell 122, preferably, the first partition 123 can be a steel plate of the water tank 121 itself , or an additional steel plate.
[0045] The first dividing plate 123 divides the inside of the housing 122 into a dust removal passage 124 and a polishing area 125; on the water tank 121 and on both sides of the first dividing plate 123, a dust inlet 126 and a dust outlet 127 are provided, that is, the dust will f...
PUM
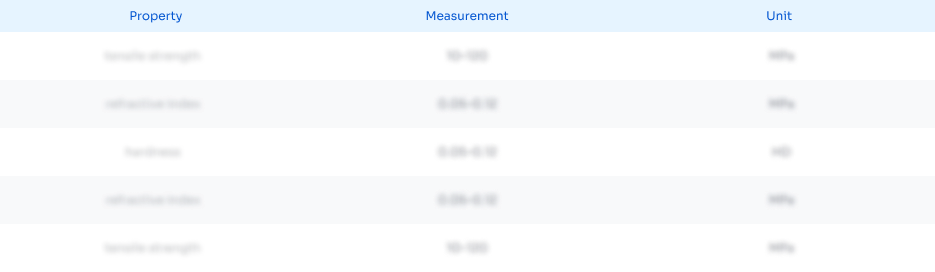
Abstract
Description
Claims
Application Information

- R&D
- Intellectual Property
- Life Sciences
- Materials
- Tech Scout
- Unparalleled Data Quality
- Higher Quality Content
- 60% Fewer Hallucinations
Browse by: Latest US Patents, China's latest patents, Technical Efficacy Thesaurus, Application Domain, Technology Topic, Popular Technical Reports.
© 2025 PatSnap. All rights reserved.Legal|Privacy policy|Modern Slavery Act Transparency Statement|Sitemap|About US| Contact US: help@patsnap.com