Step-by-step dry deacidification system and method for blast furnace gas
A technology of blast furnace gas and dry method, which is applied in separation methods, chemical instruments and methods, gas dust removal, etc., and can solve problems such as gas leakage, corrosion of auxiliary equipment, and hidden dangers of normal smelting safety in blast furnaces.
- Summary
- Abstract
- Description
- Claims
- Application Information
AI Technical Summary
Problems solved by technology
Method used
Image
Examples
Embodiment Construction
[0021] The following describes several preferred embodiments of the present invention with reference to the accompanying drawings, so as to make the technical content clearer and easier to understand. The present invention can be embodied in many different forms of embodiments, and the protection scope of the present invention is not limited to the embodiments mentioned herein.
[0022] see figure 1 , the step-by-step dry deacidification system of blast furnace gas according to the present invention comprises:
[0023] Blast furnace clean gas supply subsystem after dedusting, dehydration drying tower dehydration subsystem, inorganic acid removal tower to remove HCl, H 2 S subsystem, organic sulfur hydrolysis tower hydrolysis COS subsystem, desulfurization tower removal of H 2 S subsystem, deacidification agent replacement subsystem.
[0024] (1) Blast furnace clean gas supply subsystem after dedusting: this subsystem sends the raw gas generated on the top of the blast furna...
PUM
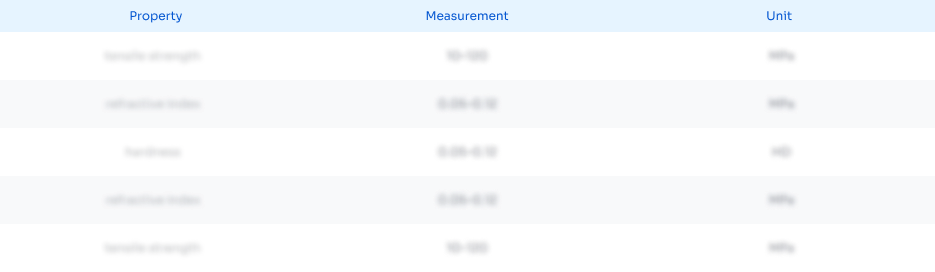
Abstract
Description
Claims
Application Information

- Generate Ideas
- Intellectual Property
- Life Sciences
- Materials
- Tech Scout
- Unparalleled Data Quality
- Higher Quality Content
- 60% Fewer Hallucinations
Browse by: Latest US Patents, China's latest patents, Technical Efficacy Thesaurus, Application Domain, Technology Topic, Popular Technical Reports.
© 2025 PatSnap. All rights reserved.Legal|Privacy policy|Modern Slavery Act Transparency Statement|Sitemap|About US| Contact US: help@patsnap.com