Manufacturing method of outer ring splicing block assembly
A manufacturing method and technology of block components, applied in the direction of manufacturing tools, metal processing machinery parts, clamping, etc., can solve problems such as processing errors, surface misalignment, large gaps in joint surfaces, etc., to improve processing efficiency, improve overall accuracy, The effect of improving the pass rate
- Summary
- Abstract
- Description
- Claims
- Application Information
AI Technical Summary
Problems solved by technology
Method used
Image
Examples
Embodiment Construction
[0032] The present invention will be further described in detail below in conjunction with the accompanying drawings and embodiments.
[0033] A method for manufacturing an outer ring block assembly, comprising the following steps:
[0034] Step 1, such as Figure 2-Figure 5 As shown, the jig plate is made, and the jig plate annular plate is divided into two types: the A-side jig plate 11 and the B-side jig plate 12, and the outer diameter of the B-side jig plate 12 is larger than the outer diameter of the A-side jig plate 11, respectively. Pin holes 9 and screw holes 10 are bored out on the plate 11 and the fixture plate 12 on the B side. The purpose of the fixture plate 11 on the A side and the fixture plate 12 on the B side is to be fixed on the A side 6 of the piece I1, the piece II2 and the piece III3. and on the B side 7, so that each piece is connected and fixed into a whole ring;
[0035] Step 2, such as Figure 6-Figure 11 As shown, each piece is blanked into a cub...
PUM
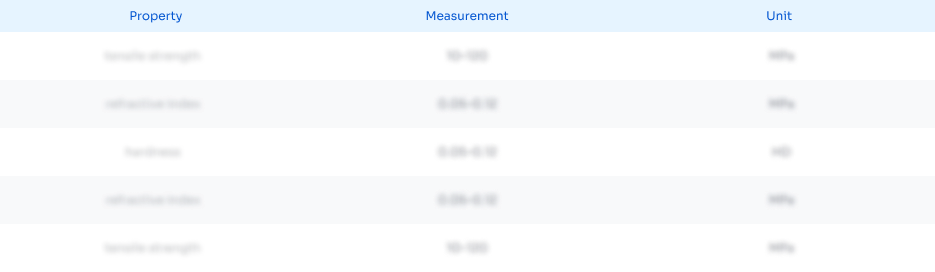
Abstract
Description
Claims
Application Information

- R&D
- Intellectual Property
- Life Sciences
- Materials
- Tech Scout
- Unparalleled Data Quality
- Higher Quality Content
- 60% Fewer Hallucinations
Browse by: Latest US Patents, China's latest patents, Technical Efficacy Thesaurus, Application Domain, Technology Topic, Popular Technical Reports.
© 2025 PatSnap. All rights reserved.Legal|Privacy policy|Modern Slavery Act Transparency Statement|Sitemap|About US| Contact US: help@patsnap.com