High-altitude climbing type welding robot based on AI visual identification
A welding robot and visual recognition technology, applied in welding equipment, auxiliary welding equipment, welding/cutting auxiliary equipment, etc., can solve problems such as high risk, and achieve the goal of ensuring production safety, increasing the effective operating range, and reducing manual labor intensity. Effect
- Summary
- Abstract
- Description
- Claims
- Application Information
AI Technical Summary
Problems solved by technology
Method used
Image
Examples
Embodiment 1
[0038] Such as Figure 1-Figure 7 As shown, a high-altitude climbing welding robot based on AI visual recognition in this embodiment includes a main body 1 of a robot arm, and connecting frames 2 are provided at the upper and lower ends of the main body 1 of the robot arm, and the connecting frames 2 are respectively controlled by rotation. The mechanism 3 is connected to the mounting base 4, and the rotation control mechanism 3 is used to drive the turning of the main body of the robot arm 1 and the mounting base 4, so as to realize the climbing process; the side of the mounting base 4 is provided with an image collector 5 for visual recognition, Moreover, a clamping portion 6 for clamping a structure is provided on a side of the mounting base 4 , and a welding mechanism 10 is provided on the outer side of the middle part of the robot arm main body 1 . The surface of the robot arm main body 1 is also equipped with an expansion board 7 for providing subsequent program function...
Embodiment 2
[0043] A high-altitude climbing welding robot based on AI visual recognition in this embodiment is basically the same as in Embodiment 1. Furthermore, in this embodiment, the clamping part 6 at each end of the robot arm body 1 has two front and rear distributions. The two sets of clamping parts 6 are composed of two groups of clamping parts 6 at the same end, which are controlled by the position control mechanism to approach or move away from each other, so as to realize the clamping and detachment of the structure. Specifically, such as Figure 5 As shown, the position control mechanism includes an adjustment rod 16 arranged on the mounting base 4, the adjustment rod 16 is connected with the second motor 17 and driven to rotate by it, the adjustment rod 16 is a two-way threaded rod, that is, two sections of opposite directions threaded segment, and the threaded segment in each direction is correspondingly threaded and installed with a drive block 15, and each drive block 15 i...
Embodiment 3
[0045] A high-altitude climbing welding robot based on AI visual recognition in this embodiment is basically the same as Embodiment 2, further, as Figure 5 and Figure 6 As shown, in the present embodiment, two sets of clamping parts 6 at the same end before and after, are equipped with two sets of limit wheels 18 on the inner sides of the opposite distribution, and the limit wheels 18 rotate between the movable shaft 19 and the clamping parts 6 Cooperate, and the two sets of limit wheels 18 are arranged symmetrically along the center line of the clamping part 6 in the length direction. Among them such as Figure 5 As shown, the movable shaft 19 of the active limiting wheel 18 is connected with the third motor 20 and driven to rotate by it, and the two groups of limiting wheels 18 are connected and synchronously driven by a synchronous connection mechanism. Specifically, the synchronous connection mechanism includes a drive belt 21 and a guide wheel 22, the movable shaft 19...
PUM
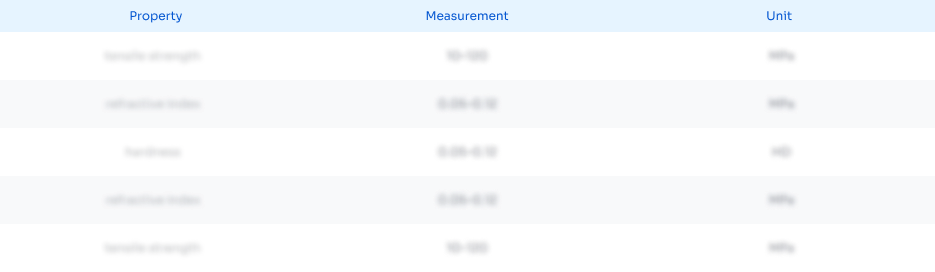
Abstract
Description
Claims
Application Information

- R&D
- Intellectual Property
- Life Sciences
- Materials
- Tech Scout
- Unparalleled Data Quality
- Higher Quality Content
- 60% Fewer Hallucinations
Browse by: Latest US Patents, China's latest patents, Technical Efficacy Thesaurus, Application Domain, Technology Topic, Popular Technical Reports.
© 2025 PatSnap. All rights reserved.Legal|Privacy policy|Modern Slavery Act Transparency Statement|Sitemap|About US| Contact US: help@patsnap.com