Thin-specification strip steel shearing method
A thin-gauge, strip-steel technology, applied in rolling mill control devices, metal rolling, manufacturing tools, etc., can solve the problem that strips cannot be threaded, and achieve the effect of reducing manual intervention, high efficiency, easy and safe operation
- Summary
- Abstract
- Description
- Claims
- Application Information
AI Technical Summary
Problems solved by technology
Method used
Image
Examples
Embodiment 1
[0035] A thin-gauge strip shearing method provided by the present invention is used for shearing the ultra-thick section at one end of the strip 1 before the finished product pass of the single-stand reversing rolling mill unit rolling, and the thickness of the ultra-thick section is Exceeding the set thickness, in this embodiment, it is stipulated that the thickness of the ultra-thick section exceeds the set thickness of the previous rolling pass, including the following steps:
[0036] The feeding roller 3 and the guide roller 4 are controlled to press the super-thick section, and the strip steel 1 moves under the linkage of the coiling mandrel 5, the guide roller 4 and the feeding roller 3 to complete rolling and coiling and feeding.
[0037] Control the movement of the strip steel 1, and the strip steel 1 is coiled under the condition of linkage of various equipments. After the ultra-thick section moves between the guide roller 4 and the coiling mandrel 5 of the rolling mil...
Embodiment 2
[0049] Based on the same inventive concept, this embodiment provides a control device, which includes a memory and a processor connected to the memory. The memory stores program codes, and the processor is used to read the program codes from the memory to execute the above-mentioned embodiment 1. In the thin-gauge steel strip shearing method, the control equipment can specifically be a PLC controller, an industrial computer, and the like. In this embodiment, an industrial computer is used.
Embodiment 3
[0051] Based on the same inventive concept, this embodiment provides a computer-readable storage medium, the computer-readable storage medium stores program codes, and when the program codes are executed by a processor, the thin-gauge strip steel shears of the above-mentioned embodiment 1 can be implemented. cut method.
[0052] Through the above-mentioned embodiments, the thin-gauge steel strip shearing method provided by the present invention has the following beneficial effects or advantages:
[0053] 1) Compared with the prior art, the thin-gauge strip shearing method provided by the present invention is realized based on the structure of the rolling mill unit itself, and the slit is threaded through the strip through the linkage operation of the rolling mill and sent between the guide roll and the coiling mandrel. Under the cooperation of the coiling force of the crimping mandrel, the friction force of the guide roller and the feeding roller on the strip steel, the incisi...
PUM
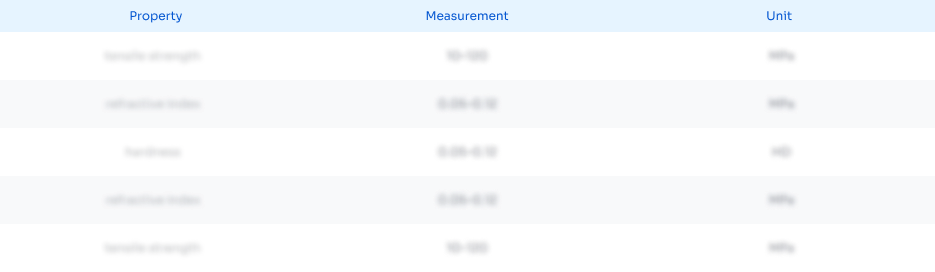
Abstract
Description
Claims
Application Information

- R&D
- Intellectual Property
- Life Sciences
- Materials
- Tech Scout
- Unparalleled Data Quality
- Higher Quality Content
- 60% Fewer Hallucinations
Browse by: Latest US Patents, China's latest patents, Technical Efficacy Thesaurus, Application Domain, Technology Topic, Popular Technical Reports.
© 2025 PatSnap. All rights reserved.Legal|Privacy policy|Modern Slavery Act Transparency Statement|Sitemap|About US| Contact US: help@patsnap.com