Steel wire heat treatment quenching process
A steel wire and process technology, applied in the field of steel wire heat treatment and quenching process, can solve the problems of high production cost, unreasonable, unreasonable schedule of total acidity and free acidity phosphating, etc., and achieve good performance effect
- Summary
- Abstract
- Description
- Claims
- Application Information
AI Technical Summary
Problems solved by technology
Method used
Examples
Embodiment Construction
[0023] The technical solutions in the embodiments of the present invention will be clearly and completely described below in conjunction with the embodiments of the present invention. Apparently, the described embodiments are only some of the embodiments of the present invention, not all of them. Based on the embodiments of the present invention, all other embodiments obtained by persons of ordinary skill in the art without making creative efforts belong to the protection scope of the present invention.
[0024] The invention provides a technical solution: a steel wire heat treatment and quenching process, including the following steps:
[0025] Step 1: The steel wire is led out through the roller of the pay-off machine, and then output horizontally after passing through the positioning device;
[0026] Step 2: Heat the steel wire to 900-950°C to transform the structure into austenite, and then melt it in molten lead or salt (sodium nitrate and potassium nitrate or calcium chl...
PUM
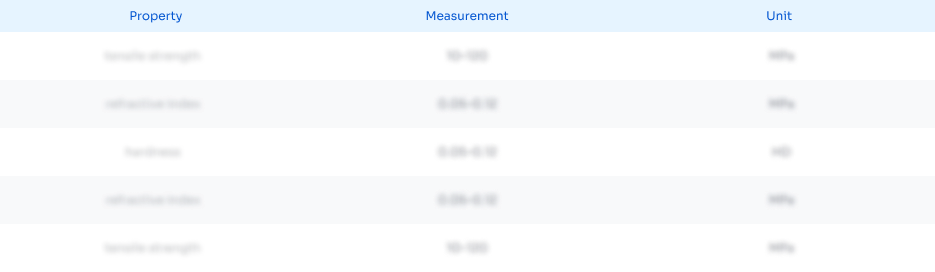
Abstract
Description
Claims
Application Information

- R&D
- Intellectual Property
- Life Sciences
- Materials
- Tech Scout
- Unparalleled Data Quality
- Higher Quality Content
- 60% Fewer Hallucinations
Browse by: Latest US Patents, China's latest patents, Technical Efficacy Thesaurus, Application Domain, Technology Topic, Popular Technical Reports.
© 2025 PatSnap. All rights reserved.Legal|Privacy policy|Modern Slavery Act Transparency Statement|Sitemap|About US| Contact US: help@patsnap.com