Hot stamping machine and working method thereof
A hot stamping machine and frame technology, applied in bag making, mechanical equipment, engine components, etc., can solve the problems of poor hot stamping effect and affecting the speed of hot stamping, and achieve good working effect and simple and fast working process Effect
- Summary
- Abstract
- Description
- Claims
- Application Information
AI Technical Summary
Problems solved by technology
Method used
Image
Examples
Embodiment 1
[0049] Such as Figures 1 to 5 As shown, the present invention provides a hot stamping machine, comprising: two upper driving rollers 100 and lower driving rollers 200 arranged parallel to each other, an upper ironing sheet 300 fixed on the upper driving roller 100, fixed on the lower driving roller 200 The lower ironing piece 400, the two ends of the lower driving roller 200 are rotatably provided with elastic parts 500. Wherein the upper driving roller 100 and the lower driving roller 200 can rotate relative to each other, and drive the hot stamping machine shown in this embodiment to switch different working states to complete different working processes; the upper hot plate 300 and the lower hot plate 400 can be rotated to relative settings position and hot stamp the film passing between the upper stamper 300 and the lower stamper 400; the elastic part 500 can reset the lower driving roller 200 after cutting the film. At the same time, during the reset process, the upper ...
PUM
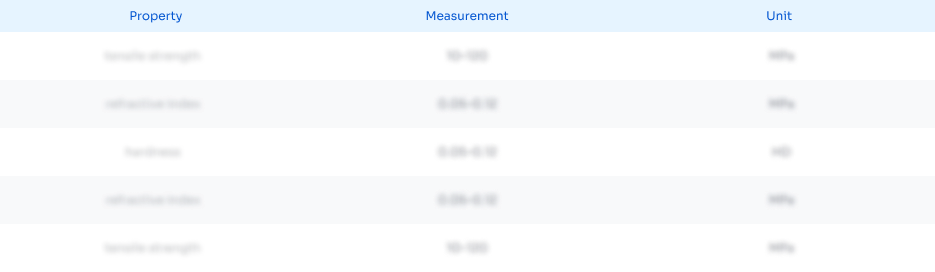
Abstract
Description
Claims
Application Information

- R&D Engineer
- R&D Manager
- IP Professional
- Industry Leading Data Capabilities
- Powerful AI technology
- Patent DNA Extraction
Browse by: Latest US Patents, China's latest patents, Technical Efficacy Thesaurus, Application Domain, Technology Topic, Popular Technical Reports.
© 2024 PatSnap. All rights reserved.Legal|Privacy policy|Modern Slavery Act Transparency Statement|Sitemap|About US| Contact US: help@patsnap.com