Method for assisting in improving glass welding strength through high-vacuum magnetron sputtering interface
A technology of vacuum magnetron sputtering and welding strength, applied in the coating and other directions, can solve the problems of low energy absorption rate, poor welding quality, unstable welding quality and so on
- Summary
- Abstract
- Description
- Claims
- Application Information
AI Technical Summary
Problems solved by technology
Method used
Image
Examples
Embodiment Construction
[0019] refer to figure 1 . According to the present invention, the front end of the high repetition rate ultrafast laser 1 of the equipment required for welding is provided with a total reflection mirror 2 with a 45° inclined surface, and the mirror symmetry is distributed along the vertical optical path along the inclined surface of the total reflection mirror 2. The reverse U-shaped optical path is formed by the figure-eight total reflection mirror; the electronically controlled three-dimensional motion platform 3, the ultrashort pulse beam generated by the high repetition rate ultrafast laser 1, changes direction through the total reflection mirror 2 and transmits to the end 45 of the reverse U-shaped optical path. ° Looking down at the total reflection mirror, the ultrafast laser beam 8 emitted vertically downward is transmitted to the aperture 10, the size of the spot is adjusted through the aperture 10, and then focused by the focusing mirror 9 onto the positioning fixtu...
PUM
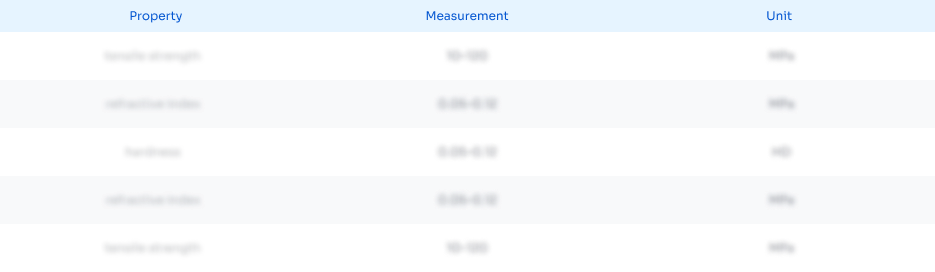
Abstract
Description
Claims
Application Information

- R&D Engineer
- R&D Manager
- IP Professional
- Industry Leading Data Capabilities
- Powerful AI technology
- Patent DNA Extraction
Browse by: Latest US Patents, China's latest patents, Technical Efficacy Thesaurus, Application Domain, Technology Topic, Popular Technical Reports.
© 2024 PatSnap. All rights reserved.Legal|Privacy policy|Modern Slavery Act Transparency Statement|Sitemap|About US| Contact US: help@patsnap.com