Magnetic-gravity-magnetic combined separation process for treating lean magnetite
A technology of lean magnetite and process, which is applied in the field of magnetic-gravity-magnetic combined beneficiation process, which can solve the problems of increasing grinding cost, lengthy and cumbersome process, and aggravated metal loss.
- Summary
- Abstract
- Description
- Claims
- Application Information
AI Technical Summary
Problems solved by technology
Method used
Image
Examples
Embodiment
[0032] Such as figure 1 As shown, a kind of magnetic-gravity-magnetic combined mineral processing process for processing lean magnetite of the present invention comprises: the magnetite ore raw ore that particle size is -12mm content 90%, grade is 25.45% is fed into one section of closed-circuit grinding operation, A graded overflow product with a -200 mesh content of 57.35% is obtained, and the primary graded overflow product is fed into a section of weak magnetic operation to obtain a section of weak magnetic concentrate and a section of weak magnetic tailings, and a section of weak magnetic tailings. In that: the first stage of weak magnetic concentrate is sequentially processed through subsequent gravity-magnetic screen combination operation, secondary grinding and classification operation and three-stage magnetic separation operation to obtain final concentrate and final tailings;
[0033] The heavy-magnetic sieve combination operation is composed of a spiral chute, a fi...
PUM
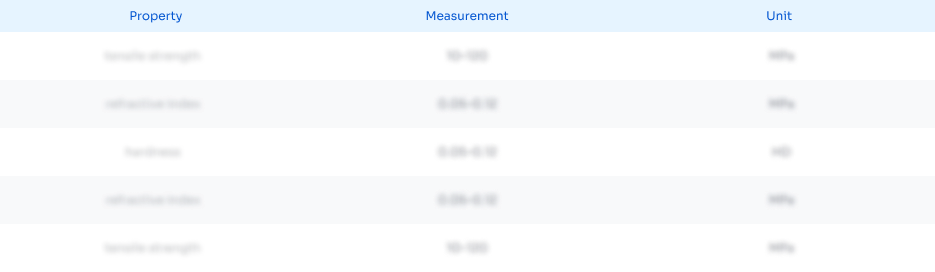
Abstract
Description
Claims
Application Information

- R&D
- Intellectual Property
- Life Sciences
- Materials
- Tech Scout
- Unparalleled Data Quality
- Higher Quality Content
- 60% Fewer Hallucinations
Browse by: Latest US Patents, China's latest patents, Technical Efficacy Thesaurus, Application Domain, Technology Topic, Popular Technical Reports.
© 2025 PatSnap. All rights reserved.Legal|Privacy policy|Modern Slavery Act Transparency Statement|Sitemap|About US| Contact US: help@patsnap.com