Hydraulic drive robot joint stepless speed change device
A technology of continuously variable speed change device and robot joint, which is applied in transmission device, gear transmission device, fluid transmission device, etc., can solve the problems of difficult to exert the optimal performance of the motor, unapplied, complex structure, etc.
- Summary
- Abstract
- Description
- Claims
- Application Information
AI Technical Summary
Problems solved by technology
Method used
Image
Examples
Embodiment Construction
[0028] In order to make the purpose, technical solutions and advantages of the embodiments of the present invention clearer, the technical solutions in the embodiments of the present invention will be clearly and completely described below in conjunction with the embodiments of the present invention. Obviously, the described embodiments are part of the present invention Examples, not all examples. Based on the embodiments of the present invention, all other embodiments obtained by persons of ordinary skill in the art without creative efforts fall within the protection scope of the present invention.
[0029] Such as Figure 1 ~ Figure 2As shown, its structural relationship is: the left end cover 13 and the right end cover 14 are respectively connected and fixed to the left and right ends of the annular cylinder 15, forming a cavity with the annular cylinder 15, and the left bracket 11 and the right bracket 12 are respectively arranged in the cavity The left and right sides of...
PUM
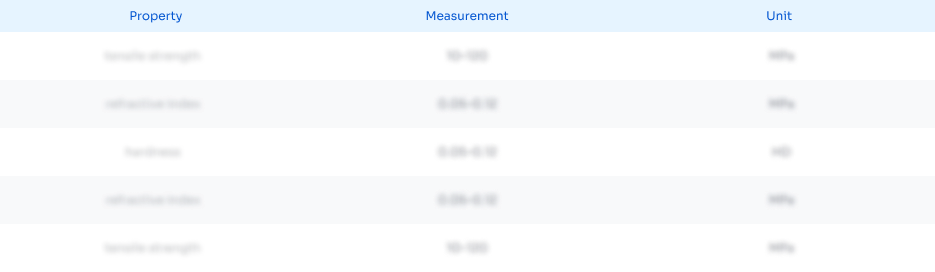
Abstract
Description
Claims
Application Information

- Generate Ideas
- Intellectual Property
- Life Sciences
- Materials
- Tech Scout
- Unparalleled Data Quality
- Higher Quality Content
- 60% Fewer Hallucinations
Browse by: Latest US Patents, China's latest patents, Technical Efficacy Thesaurus, Application Domain, Technology Topic, Popular Technical Reports.
© 2025 PatSnap. All rights reserved.Legal|Privacy policy|Modern Slavery Act Transparency Statement|Sitemap|About US| Contact US: help@patsnap.com