Wool twisting system and method
A hair-feeding and brushing technology, which is applied in the field of winching system, can solve the problems of poor quality, low density, and non-compactness of pipeline brushes
- Summary
- Abstract
- Description
- Claims
- Application Information
AI Technical Summary
Problems solved by technology
Method used
Image
Examples
Embodiment 1
[0049] see figure 1 , the embodiment of the present disclosure provides a winching system.
[0050] Specifically, see figure 1 , the winching system 100 includes: a controller 101, a hair feeding module 102 and a winching module 103;
[0051] The hair-feeding module 102 includes a hair-feeding servo driver 1021, a hair-feeding motor 1022 electrically connected to the hair-feeding servo driver 1021, and a hair-feeding mechanism 1023 connected to the hair-feeding shaft of the hair-feeding motor 1022;
[0052] The stranding module 103 includes a stretching servo driver 1031, a rotating servo driver 1033, a rotating cylinder 1035, a stretching motor 1032 electrically connected to the stretching servo driver 1031, a rotating motor electrically connected to the rotating servo driver 1033 1034, the stretching motor 1032 includes a stretching shaft, and the rotating motor 1034 includes a rotating shaft;
[0053] The controller 101 is electrically connected to the hair-feeding servo...
Embodiment 2
[0082] In addition, an embodiment of the present disclosure provides a method of winching, which is applied to the winching system provided in Embodiment 1.
[0083] Specifically, such as Figure 8 As shown, the winching method includes:
[0084] Step S801, when the stretching servo driver controls the stretching shaft to drive the material filament held by the rotating cylinder to move along the stretching direction, the hair-feeding shaft is controlled by the hair-feeding servo driver to synchronously drive the hair-feeding mechanism, and the hair-feeding mechanism is put on the The bristles are placed on the filament;
[0085] Step S802 , controlling the rotating shaft to rotate synchronously by rotating the servo driver, driving the filament to rotate, and twisting the bristles placed on the filament into the filament.
[0086] Optionally, step S801 includes: when the stretching servo driver is used to control the stretching shaft to drive the filament to move along the ...
PUM
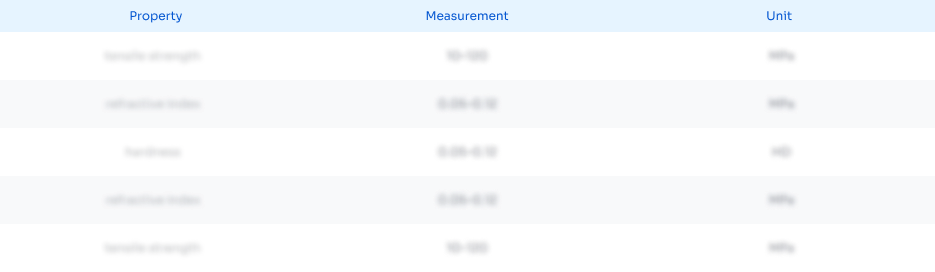
Abstract
Description
Claims
Application Information

- R&D
- Intellectual Property
- Life Sciences
- Materials
- Tech Scout
- Unparalleled Data Quality
- Higher Quality Content
- 60% Fewer Hallucinations
Browse by: Latest US Patents, China's latest patents, Technical Efficacy Thesaurus, Application Domain, Technology Topic, Popular Technical Reports.
© 2025 PatSnap. All rights reserved.Legal|Privacy policy|Modern Slavery Act Transparency Statement|Sitemap|About US| Contact US: help@patsnap.com