Air film cooling composite hole structure for turbine blade and turbine blade
A technology of turbine blade and air film cooling, which is applied in the direction of supporting elements of blades, machines/engines, mechanical equipment, etc., can solve the problem of low diffusion capacity of air film jet flow in the span direction, achieve excellent cooling effect, improve cooling effect, and enhance The effect of lateral spreading ability
- Summary
- Abstract
- Description
- Claims
- Application Information
AI Technical Summary
Problems solved by technology
Method used
Image
Examples
Embodiment 1
[0041] The dumbbell-shaped groove film cooling compound hole structure of the turbine blade in this embodiment, such as Figure 5 As shown, the pressure surface of the turbine blade is processed with a dumbbell-shaped groove air film hole 10 on the pressure surface, and the suction surface is processed with a dumbbell-shaped groove air film hole 11 on the suction surface, and the air is supplied by the internal cooling channel 12; A dumbbell-shaped groove is provided at the outlet of the composite gas film hole 4 . Wherein the structure of the compound air film hole 4 is composed of a spanwise expansion section 8 and a straight hole section 9, and the diameter of the straight hole section 9 is D h The value is 1mm, and the length of the straight hole section 9 is L 1 2mm, length L of spanwise expansion section 8 2 The size is 6mm, the spanwise expansion angle β is 10°, and the gas film hole flow direction inclination angle θ is 35°. The angle α between the side of the dumbb...
Embodiment 2
[0044] The air film hole 10 is processed on the pressure surface with a dumbbell-shaped groove on the pressure surface, and the air film hole 11 is processed on the suction surface with a dumbbell-shaped groove on the suction surface, and the air is supplied by the internal cooling channel 12; There are dumbbell-shaped grooves in the part. Wherein the structure of the compound air film hole 4 is composed of a spanwise expansion section 8 and a straight hole section 9, and the diameter of the straight hole section 9 is D h The value is 0.5mm, and the length of the straight hole section 9 is L 1 2.99mm, spanwise expansion section 8 length L 2 The size is 3mm, the spanwise expansion angle β is 15°, and the gas film hole flow direction inclination angle θ is 50°. The angle α between the side of the dumbbell-shaped groove and the flow direction of the mainstream gas A is 80°, the throat of the groove is flush with the front and rear edges of the outlet of the composite gas film h...
PUM
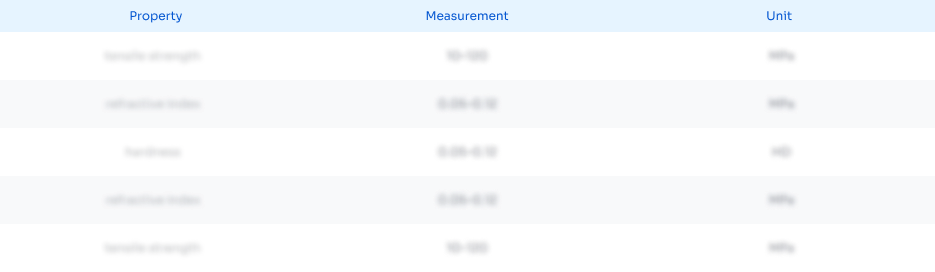
Abstract
Description
Claims
Application Information

- R&D Engineer
- R&D Manager
- IP Professional
- Industry Leading Data Capabilities
- Powerful AI technology
- Patent DNA Extraction
Browse by: Latest US Patents, China's latest patents, Technical Efficacy Thesaurus, Application Domain, Technology Topic, Popular Technical Reports.
© 2024 PatSnap. All rights reserved.Legal|Privacy policy|Modern Slavery Act Transparency Statement|Sitemap|About US| Contact US: help@patsnap.com