Spot welding robot operation space smooth path planning method for curved surface workpiece
A technology for path planning and surface workpieces, which is applied in instruments, digital control, control/regulation systems, etc., and can solve problems such as the inability to obtain the global optimal solution of the welding path.
- Summary
- Abstract
- Description
- Claims
- Application Information
AI Technical Summary
Problems solved by technology
Method used
Image
Examples
Embodiment Construction
[0021] Attached below Figure 1-15 The present invention is described in further detail,
[0022] Such as figure 1 As shown, the transformation matrix of the robot link is as follows:
[0023]
[0024] In the formula, a i-1 is the connecting rod length, α i-1 is the connecting rod twist angle, d i is the connecting rod offset, θ i is the joint angle. cθ i represents cosθ i , sθ i Indicates sinθ i , cα i-1 means cosα i-1 , sα i-1 Indicates sinα i-1 .
[0025] due to a i-1 、α i-1 、d i are known quantities, so the joint transformation matrix Only with the joint variable θ i Relevant, therefore, the following formulas, unless otherwise specified, c i represents cosθ i ,s i Indicates sinθ i .
[0026] The pose of the end coordinate system of the robot in the base coordinates is described by a homogeneous transformation matrix, and the positive solution expression of the robot kinematics is:
[0027]
[0028] In the formula, θ includes (θ 1 ,θ 2 ,θ ...
PUM
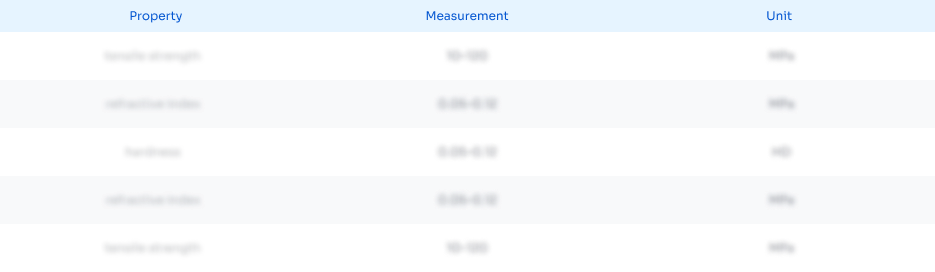
Abstract
Description
Claims
Application Information

- R&D
- Intellectual Property
- Life Sciences
- Materials
- Tech Scout
- Unparalleled Data Quality
- Higher Quality Content
- 60% Fewer Hallucinations
Browse by: Latest US Patents, China's latest patents, Technical Efficacy Thesaurus, Application Domain, Technology Topic, Popular Technical Reports.
© 2025 PatSnap. All rights reserved.Legal|Privacy policy|Modern Slavery Act Transparency Statement|Sitemap|About US| Contact US: help@patsnap.com