Turbine moving blade internal composite cooling structure
A composite cooling and moving blade technology, applied in engine components, engine functions, machines/engines, etc., can solve problems such as difficult to achieve cooling effect, and achieve the effect of enhancing fluid turbulent kinetic energy, improving heat transfer level, and reducing resistance loss
- Summary
- Abstract
- Description
- Claims
- Application Information
AI Technical Summary
Problems solved by technology
Method used
Image
Examples
Embodiment Construction
[0036] The present invention will be further described below in conjunction with accompanying drawing:
[0037] refer to Figure 1 to Figure 6 , a composite cooling structure inside a turbine blade provided by the present invention, comprising a swirl cooling channel 1, a U-shaped cooling channel 3 and a trailing edge trapezoidal cooling channel 7, a U-shaped cooling channel inlet section 5 of the U-shaped cooling channel 3 and The outlet section 6 of the U-shaped cooling channel communicates with the swirl cooling channel 1 through several jet holes 2 . The swirling flow cooling channel 1, the U-shaped cooling channel 3 and the trailing edge trapezoidal cooling channel 7 are arranged on the surface with a number of ball sockets 8 / ball convexes 11 and air film holes 10 structures, and the U-shaped cooling channel 3 and the trailing edge trapezoidal cooling channel 7 are arranged There are several fin 9 structures.
[0038] refer to Figure 3 to Figure 6, the shape of the ta...
PUM
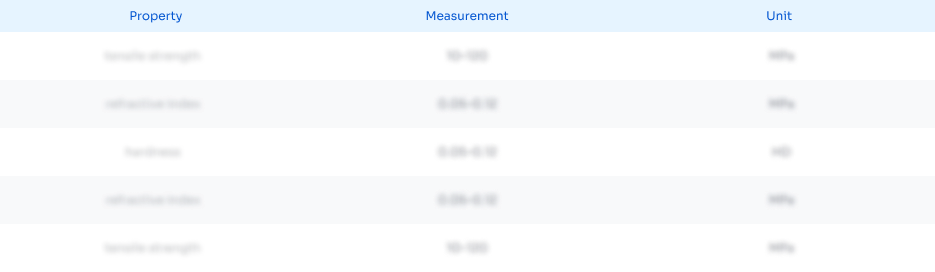
Abstract
Description
Claims
Application Information

- R&D
- Intellectual Property
- Life Sciences
- Materials
- Tech Scout
- Unparalleled Data Quality
- Higher Quality Content
- 60% Fewer Hallucinations
Browse by: Latest US Patents, China's latest patents, Technical Efficacy Thesaurus, Application Domain, Technology Topic, Popular Technical Reports.
© 2025 PatSnap. All rights reserved.Legal|Privacy policy|Modern Slavery Act Transparency Statement|Sitemap|About US| Contact US: help@patsnap.com