Macroscopic deployment robot system and method for dust-free workshop
A robot system and clean room technology, applied in the field of intelligent robots, can solve the problems of complex development of magnetic strip navigation path, change or expansion, affect the overall appearance of the workshop, and destroy the clean environment of the workshop, so as to shorten the invalid moving distance, The data transmission is accurate and fast, and the effect of reducing the influence of the robot signal
- Summary
- Abstract
- Description
- Claims
- Application Information
AI Technical Summary
Problems solved by technology
Method used
Image
Examples
Embodiment Construction
[0065] The present invention will be further described in detail below in conjunction with the accompanying drawings and embodiments. It should be understood that the specific embodiments described here are only used to explain the present invention, but not to limit the present invention. In addition, it should be noted that, for the convenience of description, only some structures related to the present invention are shown in the drawings but not all structures.
[0066] An embodiment of the present invention provides a macro deployment robot system for a clean room. figure 1 It is a schematic structural diagram of a macro deployment robot system in a clean room provided by an embodiment of the present invention. see figure 1 , the system includes: a server 100, an automation device 200 and a robot 300. The server 100 is configured to receive task instructions, and send the received task instructions to automation equipment 200 or charging piles and other equipment. Exem...
PUM
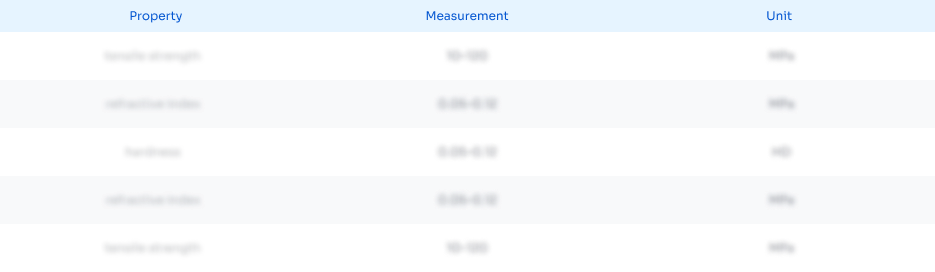
Abstract
Description
Claims
Application Information

- R&D
- Intellectual Property
- Life Sciences
- Materials
- Tech Scout
- Unparalleled Data Quality
- Higher Quality Content
- 60% Fewer Hallucinations
Browse by: Latest US Patents, China's latest patents, Technical Efficacy Thesaurus, Application Domain, Technology Topic, Popular Technical Reports.
© 2025 PatSnap. All rights reserved.Legal|Privacy policy|Modern Slavery Act Transparency Statement|Sitemap|About US| Contact US: help@patsnap.com