Method for improving absolute positioning precision based on six-degree-of-freedom series mechanical arm
A technology of absolute positioning accuracy and manipulators, which is applied in the direction of manipulators, program-controlled manipulators, manufacturing tools, etc., and can solve problems such as impact, structural mismatch, and restrictions on high-precision tasks of manipulators
- Summary
- Abstract
- Description
- Claims
- Application Information
AI Technical Summary
Problems solved by technology
Method used
Image
Examples
specific Embodiment
[0099] Such as figure 1 As shown in the figure, the scene of industrial manipulator calibration is selected to implement the technical solution. The equipment consists of a manipulator, a laser tracker, and a fixed value clamp for holding the target. The target is installed at the end of the manipulator to measure the end point. , where the nominal rod length parameter of the manipulator is known, and the parameters of the connecting rod of the manipulator are as follows figure 2 As shown, the sixth axis rod length information is set to 0, and the remaining axes are set to
[0100] l 1 =455mm, l 2 =592mm, l 3 =153mm, l 4 =638mm, l 5 =193mm, l 6 = 150mm. The robotic arm is calibrated and returned to zero before leaving the factory. At the same time, the length of the fixture is known, and the installed fixture is guaranteed to be concentric with the end flange.
[0101] First rotate the 5-axis, fit the center of the arc on the plane, find the radius of the arc, and ge...
PUM
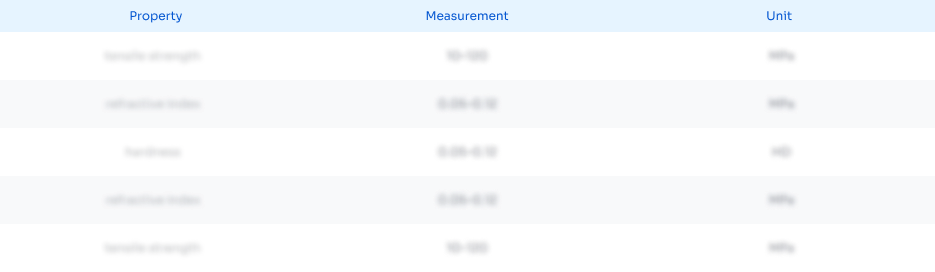
Abstract
Description
Claims
Application Information

- R&D
- Intellectual Property
- Life Sciences
- Materials
- Tech Scout
- Unparalleled Data Quality
- Higher Quality Content
- 60% Fewer Hallucinations
Browse by: Latest US Patents, China's latest patents, Technical Efficacy Thesaurus, Application Domain, Technology Topic, Popular Technical Reports.
© 2025 PatSnap. All rights reserved.Legal|Privacy policy|Modern Slavery Act Transparency Statement|Sitemap|About US| Contact US: help@patsnap.com