A bobbin counterweight method and bobbin packaging line
A technology of bobbin and counterweight, applied in packaging, transportation packaging, packaging protection and other directions, can solve the problems of heavy workload of workers, difficult to guarantee packaging accuracy and quality, low packaging efficiency, etc., to improve transportation efficiency and high processing efficiency. , the effect of easy packaging
- Summary
- Abstract
- Description
- Claims
- Application Information
AI Technical Summary
Problems solved by technology
Method used
Image
Examples
Embodiment 1
[0048] like figure 1 As shown in the figure, a bobbin yarn counterweight mechanism includes a feeding belt 11 for conveying the bobbin yarn 314, a weighing device, a counterweight belt 14 and a counterweight buffer finishing belt 15, which are arranged in sequence, and the feeding belt 11 or weighing The device sets a merging area 12. The merging area 12 can also be understood as an independent conveyor belt between the feeding belt 11 and the weighing belt 13. Between the end of the weighting belt 14 and the merging area 12, there is a conveyor belt that enables the yarn 314 to be transferred to the merging area 12. The return belt 16, the counterweight belt 14 and the return belt 16 can also be understood as different sections of the entire conveyor belt structure. The junction area 12 can be as Figure 15 and Figure 16 As shown, it is arranged on the loading belt 11, so that the package yarn 314 transferred back by the return belt 16 enters the package yarn queue of the ...
Embodiment 2
[0059] The difference between this embodiment and Embodiment 1 is that the merging area 12 is set on the counterweight belt 14, or the merging area 12 is an independent conveyor belt between the weighing belt 13 and the counterweight belt 14, and the basic work of the counterweight mechanism The principle is similar to the above case, the difference is that the package yarn 314 transferred from the return belt 16 to the confluence area 12 is no longer weighed, and is directly transferred to the counterweight belt 14 to participate in the counterweight process again.
Embodiment 3
[0061] The difference between this embodiment and the above-mentioned embodiments is that, as Figure 4 and Figure 5 As shown, the weighing device is a weighing table 132 between the feeding belt 11 and the return belt 16, a weighing device is arranged below the weighing table 132, and a yarn feeding cylinder 134 is arranged on the returning fixed frame 163 for the feeding belt The package 314 on the 11 is pushed to the merging area 12 upstream of the weighing platform 132, and the return cylinder 164 pushes the package 314 on the return belt 16 to the merging area 12, waiting for weighing, saving the package 314 on the feeding belt 11 and the waiting time for weighing on the return belt 16. The upper weighing cylinder 135 on the side of the return fixing frame 163 pushes the package 314 on the confluence area 12 to the weighing table 132 for weighing, and at the same time pushes the packaged yarn 314 from the weighing table 132 to the weighing table 132. The weight belt 14...
PUM
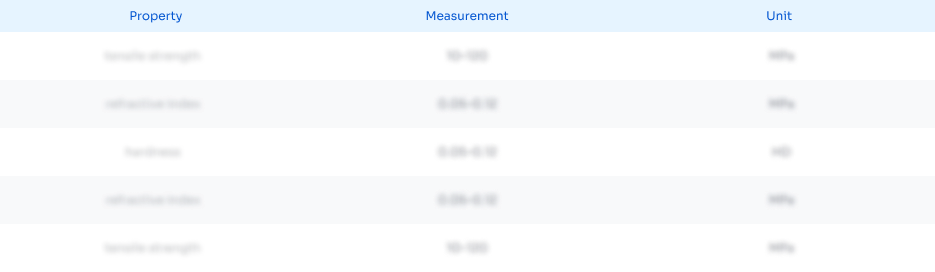
Abstract
Description
Claims
Application Information

- Generate Ideas
- Intellectual Property
- Life Sciences
- Materials
- Tech Scout
- Unparalleled Data Quality
- Higher Quality Content
- 60% Fewer Hallucinations
Browse by: Latest US Patents, China's latest patents, Technical Efficacy Thesaurus, Application Domain, Technology Topic, Popular Technical Reports.
© 2025 PatSnap. All rights reserved.Legal|Privacy policy|Modern Slavery Act Transparency Statement|Sitemap|About US| Contact US: help@patsnap.com