Full-automatic hot press molding device for multi-layer composite epoxy glass fiber plate
A technology of thermoforming and epoxy glass fiber, which is applied in the direction of flat products, household appliances, and other household appliances, etc., and can solve problems such as low efficiency of thermocompression, large change of down pressure, and non-continuous production.
- Summary
- Abstract
- Description
- Claims
- Application Information
AI Technical Summary
Problems solved by technology
Method used
Image
Examples
Embodiment Construction
[0027] The following will clearly and completely describe the technical solutions in the embodiments of the present invention with reference to the accompanying drawings in the embodiments of the present invention. Obviously, the described embodiments are only some, not all, embodiments of the present invention. Based on the embodiments of the present invention, all other embodiments obtained by persons of ordinary skill in the art without making creative efforts belong to the protection scope of the present invention.
[0028] see Figure 1-6 , the present invention provides technical solutions:
[0029] A fully automatic hot-press forming device for multi-layer composite epoxy glass fiber boards, comprising a spinning assembly 1, a tray 2, on which a composite sheet 9 to be hot-pressed is placed, the spinning assembly 1 has a rotary drive, and the spinning The pressing assembly 1 heats while applying pressure to the upper surface of the composite board 9 . Such as figure ...
PUM
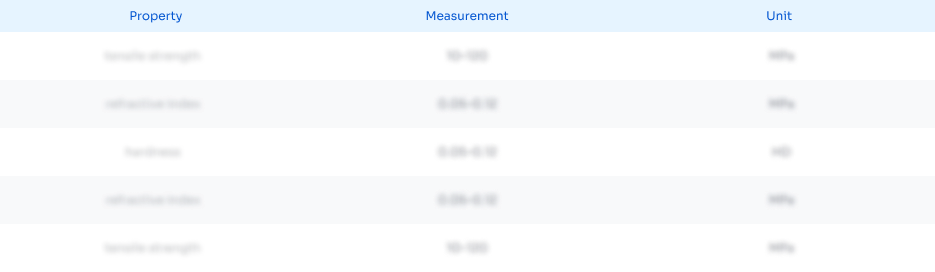
Abstract
Description
Claims
Application Information

- R&D
- Intellectual Property
- Life Sciences
- Materials
- Tech Scout
- Unparalleled Data Quality
- Higher Quality Content
- 60% Fewer Hallucinations
Browse by: Latest US Patents, China's latest patents, Technical Efficacy Thesaurus, Application Domain, Technology Topic, Popular Technical Reports.
© 2025 PatSnap. All rights reserved.Legal|Privacy policy|Modern Slavery Act Transparency Statement|Sitemap|About US| Contact US: help@patsnap.com