Visual inertial odometer method and system for calibrating equipment parameters on line
A technology of equipment parameters and odometer, which is applied in the field of computer vision, can solve problems such as application limitations, and achieve the effects of universal process, easy to use online operation process, and improved performance
- Summary
- Abstract
- Description
- Claims
- Application Information
AI Technical Summary
Problems solved by technology
Method used
Image
Examples
Embodiment 1
[0072] This embodiment provides a visual-inertial odometry method for online calibration of device parameters. The device parameters include camera external parameters, IMU bias and camera internal parameters. Please refer to figure 1 , the method includes:
[0073] S1: collect image data and IMU data through the device; specifically, the device collects image data in real time through an equipped camera, and collects IMU data in real time through an equipped IMU, and the IMU data includes gyroscope data and acceleration data;
[0074] S2: Using a Kalman filter to calibrate the camera extrinsics and the bias of the IMU online according to the image data and IMU data and calculate the pose of the image frame in the image data; specifically, the camera extrinsics include the IMU to The translation and rotation of the camera, the bias of the IMU includes the bias of the accelerometer and the bias of the gyroscope. Since the conversion relationship between the IMU and the camera i...
Embodiment 2
[0130] This embodiment provides a visual-inertial odometer system for online calibration of equipment parameters, please refer to figure 2 , the visual-inertial odometry system includes a memory 11 and a processor 12, wherein:
[0131] The memory 11 is used to store codes and related data;
[0132] The processor 12 is used to call the data in the memory 11 and execute the code in the memory 11; executing the code in the memory 11 can implement the method and steps of the aforementioned visual-inertial odometer for online calibration of equipment parameters For specific methods and steps, refer to the descriptions of the foregoing embodiments, and details are not repeated here.
[0133] In this embodiment, the memory 11 may include a volatile memory, for example, a random access memory (random access memory, RAM), and the RAM may include a static RAM or a dynamic RAM. The memory 11 may also include a non-volatile memory (non-volatile memory), such as a read-only memory (read...
Embodiment 3
[0136] This embodiment provides another visual-inertial odometry system for online calibration of device parameters. The device parameters include camera external parameters, IMU bias and camera internal parameters. Please refer to image 3 , the visual-inertial odometer system includes a data acquisition module 21, a bias calibration module 22 of the camera external reference and the IMU and a camera internal reference calibration module 23, wherein:
[0137] The data collection module 21 is used to collect image data and IMU data; specifically, the device collects image data in real time through an equipped camera, and collects IMU data in real time through an equipped IMU;
[0138]The bias calibration module 22 of the external parameters of the camera and the IMU is used to use a Kalman filter to calibrate the external parameters of the camera and the bias of the IMU online according to the image data and the IMU data and calculate the position of the image frame in the imag...
PUM
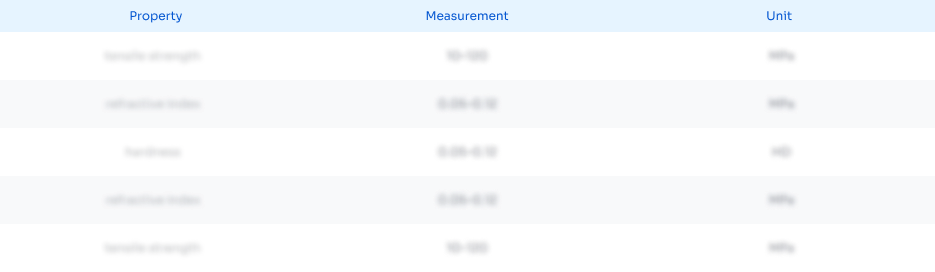
Abstract
Description
Claims
Application Information

- R&D
- Intellectual Property
- Life Sciences
- Materials
- Tech Scout
- Unparalleled Data Quality
- Higher Quality Content
- 60% Fewer Hallucinations
Browse by: Latest US Patents, China's latest patents, Technical Efficacy Thesaurus, Application Domain, Technology Topic, Popular Technical Reports.
© 2025 PatSnap. All rights reserved.Legal|Privacy policy|Modern Slavery Act Transparency Statement|Sitemap|About US| Contact US: help@patsnap.com