Calibration device and method and depth camera
A calibration device and a calibration method technology, applied in the field of computer vision, can solve problems such as the complexity of the calibration process, and achieve the effects of simplifying the calibration process, improving computing efficiency, and simplifying acquisition
- Summary
- Abstract
- Description
- Claims
- Application Information
AI Technical Summary
Problems solved by technology
Method used
Image
Examples
Embodiment 1
[0032] figure 1A schematic structural diagram of a calibration device 10 provided by an embodiment of the present application is shown, the calibration device 10 is used to calibrate a camera 00, and the calibration device 10 includes a calibration board 11, a moving part 12, a fixed bracket 13, a projection part 14 and a processor 15, the calibration plate 11 is fixed on the moving part 12, and the moving part 12 is used to change the position of the calibration plate 11; the camera 00 and the projection part 14 are fixed on the fixed bracket 13, so that the shooting of the camera 00 The picture includes the calibration plate 11; the processor 15 is electrically connected to the moving part 12 and the camera 00, and is used to receive the first calibration image and the second calibration image collected from the camera 00, and the processor 15 is also used to control The moving part 12 moves, and the internal parameters of the camera 00 and the external parameters of the cam...
Embodiment 2
[0039] The present application also provides a calibration method. In this embodiment, the process of the above calibration method is executed by a calibration device. The calibration device 10 includes a calibration board 11, a moving part 12, a fixed support 13, a projection part 14 and a processor 15, and the interconnection relationship between each part can be referred to the relevant description of the previous embodiment, and the calibration device 10 can execute the present invention. The calibration method provided by the application.
[0040] image 3 It shows the implementation flowchart of the calibration method provided by the first embodiment of the application, which is applied to figure 1 The calibration device 10 shown is described in detail as follows:
[0041] S301: Using the moving component to control the calibration plate to move to a plurality of different preset fixed positions.
[0042] In this embodiment, the calibration device can adjust the pose ...
PUM
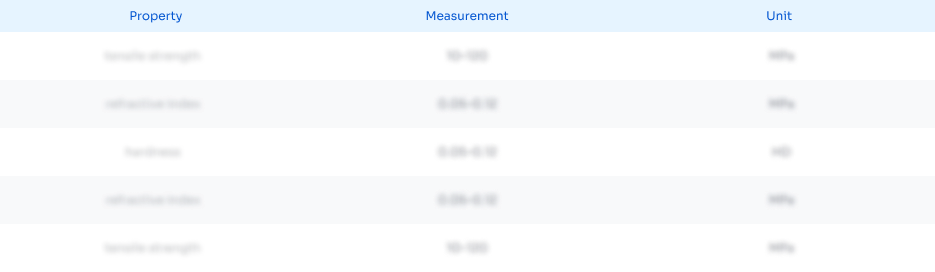
Abstract
Description
Claims
Application Information

- R&D
- Intellectual Property
- Life Sciences
- Materials
- Tech Scout
- Unparalleled Data Quality
- Higher Quality Content
- 60% Fewer Hallucinations
Browse by: Latest US Patents, China's latest patents, Technical Efficacy Thesaurus, Application Domain, Technology Topic, Popular Technical Reports.
© 2025 PatSnap. All rights reserved.Legal|Privacy policy|Modern Slavery Act Transparency Statement|Sitemap|About US| Contact US: help@patsnap.com