Modified carbon fiber, preparation method thereof and modified carbon fiber reinforced cement-based material
A fiber-reinforced cement and carbon fiber technology, which is applied in the direction of climate sustainability, bulk chemical production, sustainable waste treatment, etc., can solve the problems of poor dispersion and low bond strength, and achieve improved bond strength and density , Improve the effect of dispersion
- Summary
- Abstract
- Description
- Claims
- Application Information
AI Technical Summary
Problems solved by technology
Method used
Image
Examples
Embodiment 1
[0039] The modified carbon fiber preparation process in the present embodiment is as follows:
[0040] (1) Removal of epoxy coating on carbon fiber surface
[0041] Take 1g of carbon fiber and put it into a Soxhlet extractor filled with acetone, and use acetone to wash and remove impurities on the surface of carbon fiber at a temperature of 75°C. The cleaning time is 24 hours. Dry at 70°C for 2 hours to obtain carbon fibers with the epoxy coating removed.
[0042] (2) Oxidation of carbon fiber
[0043] Step 21, immersing the carbon fiber obtained in step (1) in concentrated nitric acid, the mass ratio of the carbon fiber to the concentrated nitric acid is 1g:100ml, heating to 80°C, reacting for 3h, and then taking out the carbon fiber in the concentrated nitric acid;
[0044] Step 22: Soak the carbon fibers obtained in Step 21 in distilled water for 5 minutes, rinse them with ethanol three times after taking them out, and dry them for 3 hours at a temperature of 70° C. to ob...
Embodiment 2
[0058] The modified carbon fiber preparation process in the present embodiment is as follows:
[0059] (1) Removal of epoxy coating on carbon fiber surface
[0060] Take 1g of carbon fiber and put it into a Soxhlet extractor filled with acetone, and use acetone to wash and remove impurities on the surface of carbon fiber at a temperature of 75°C. The cleaning time is 24 hours. Dry at 70°C for 2 hours to obtain carbon fibers with the epoxy coating removed.
[0061] (2) Oxidation of carbon fiber
[0062] Step 21, immersing the carbon fiber obtained in step (1) in concentrated nitric acid, the mass ratio of the carbon fiber to the concentrated nitric acid is 1g:100ml, heating to 80°C, reacting for 3h, and then taking out the carbon fiber in the concentrated nitric acid;
[0063] Step 22: Soak the carbon fibers obtained in Step 21 in distilled water for 5 minutes, rinse them with ethanol three times after taking them out, and dry them for 3 hours at a temperature of 70° C. to ob...
PUM
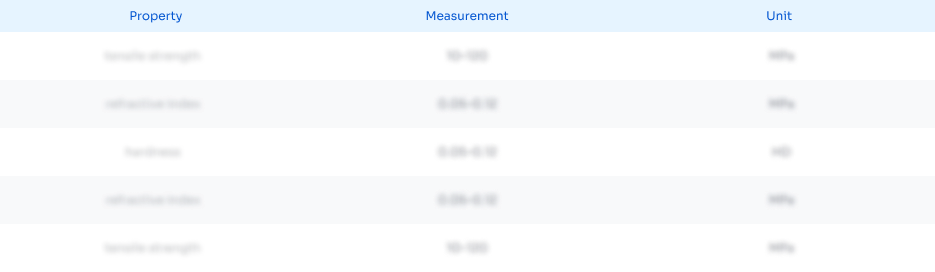
Abstract
Description
Claims
Application Information

- R&D
- Intellectual Property
- Life Sciences
- Materials
- Tech Scout
- Unparalleled Data Quality
- Higher Quality Content
- 60% Fewer Hallucinations
Browse by: Latest US Patents, China's latest patents, Technical Efficacy Thesaurus, Application Domain, Technology Topic, Popular Technical Reports.
© 2025 PatSnap. All rights reserved.Legal|Privacy policy|Modern Slavery Act Transparency Statement|Sitemap|About US| Contact US: help@patsnap.com