Paint dipping and drying integrated equipment
An integrated technology of dipping paint, applied to the device for coating liquid on the surface, pretreatment surface, spray device, etc., can solve the problems of low work efficiency, damage to the paint layer on the surface of the iron core, and cumbersome putting in and taking out. , to achieve the effect of improving production efficiency
- Summary
- Abstract
- Description
- Claims
- Application Information
AI Technical Summary
Problems solved by technology
Method used
Image
Examples
Embodiment Construction
[0052] In order to make the objectives, technical solutions and beneficial effects of the present invention clearer, the technical solutions in the embodiments of the present invention will be clearly and completely described below in conjunction with the accompanying drawings in the embodiments of the present invention. Obviously, the described embodiments It is only some embodiments of the present invention, but not all embodiments.
[0053] Such as figure 1 As shown, the integrated paint dipping and drying equipment includes iron core feeding and moving group mechanism 3, paint dipping device, air extraction device, electric control cabinet, drying device and unloading group mechanism 4, iron core feeding and moving group mechanism 3 is placed at the front end of the drying device, and the unloading group mechanism 4 is placed at the back end of the drying device. An electric control device is installed in the electric control cabinet, and the iron core feeding and moving g...
PUM
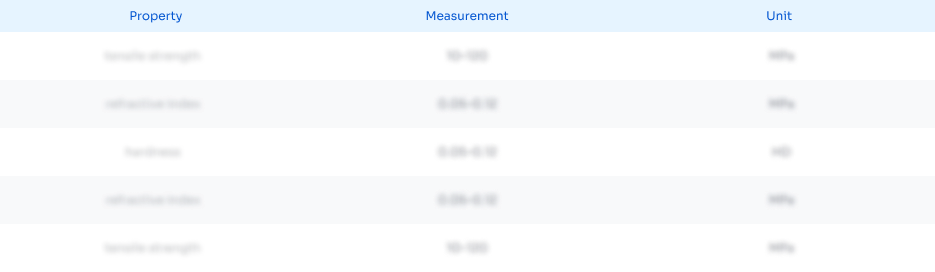
Abstract
Description
Claims
Application Information

- R&D Engineer
- R&D Manager
- IP Professional
- Industry Leading Data Capabilities
- Powerful AI technology
- Patent DNA Extraction
Browse by: Latest US Patents, China's latest patents, Technical Efficacy Thesaurus, Application Domain, Technology Topic, Popular Technical Reports.
© 2024 PatSnap. All rights reserved.Legal|Privacy policy|Modern Slavery Act Transparency Statement|Sitemap|About US| Contact US: help@patsnap.com