A method for automatic determination of compensation coefficient by peristaltic pump
A compensation coefficient, peristaltic pump technology, applied in the direction of pump, pump control, machine/engine, etc., can solve the problem that peristaltic pump does not have automatic compensation, restrict the use range of peristaltic pump, increase the workload of personnel, etc. The effect of reducing corporate burden and improving work efficiency
- Summary
- Abstract
- Description
- Claims
- Application Information
AI Technical Summary
Problems solved by technology
Method used
Image
Examples
Embodiment Construction
[0021] The following combined attachment figure 1 and figure 2 And the specific embodiment made a detailed explanation of the present invention.
[0022] The present invention provides a method of automatic measurement compensation coefficient of peristaltic pump, involving a reagent setting system, which includes reagent bottle 1. The first fiber sensor 2. The second fiber sensor 3. Main controller 4. Creation motility Pump 6, raw liquid barrel 7 and human -machine interface 5, this method includes the following steps:
[0023] S1 Preparation: For example figure 1 Show, the main controller 4 is connected to the first fiber fiber sensor 2. The second fiber sensor 3 and the peristaltic pump 6. Place the two first fiber sensors 2 symmetrical on both sides of the reagent bottle. Place on both sides of 1 bottle mouth of the reagent bottle, the creep pump 6 connects the original liquid barrel 7, the original liquid barrel 7 connecting reagent bottle 1;
[0024] S2 power -up initializat...
PUM
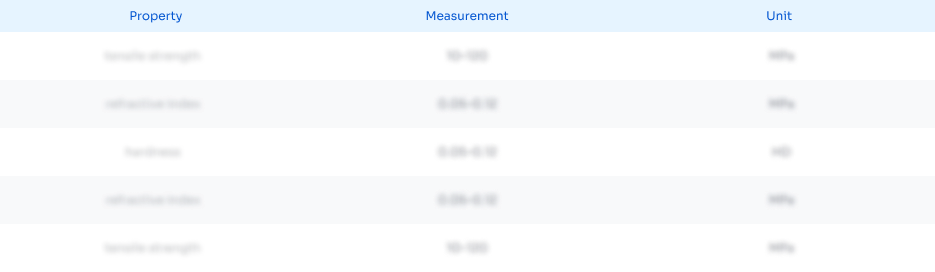
Abstract
Description
Claims
Application Information

- R&D
- Intellectual Property
- Life Sciences
- Materials
- Tech Scout
- Unparalleled Data Quality
- Higher Quality Content
- 60% Fewer Hallucinations
Browse by: Latest US Patents, China's latest patents, Technical Efficacy Thesaurus, Application Domain, Technology Topic, Popular Technical Reports.
© 2025 PatSnap. All rights reserved.Legal|Privacy policy|Modern Slavery Act Transparency Statement|Sitemap|About US| Contact US: help@patsnap.com