Atomic layer deposition equipment with multiple furnace tubes
An atomic layer deposition and furnace tube technology, applied in coating, metal material coating process, gaseous chemical plating, etc., can solve the problem of high equipment cost
- Summary
- Abstract
- Description
- Claims
- Application Information
AI Technical Summary
Problems solved by technology
Method used
Image
Examples
Embodiment 1
[0018] Such as figure 1 As shown, an atomic layer deposition equipment with multiple furnace tubes includes two furnace tubes 1, the tail end of each furnace tube 1 is connected to a main pipeline 2 through a connecting pipe, and the other end of the main pipeline 2 is connected to a vacuum pump 3.
[0019] working principle:
[0020] The length of each furnace tube is shorter than that of conventional furnace tubes, and the total length of the two furnace tubes is longer than that of conventional furnace tubes. This combination can increase the total amount of silicon wafers inside the process chamber, and the process gas The stroke of the vacuum pump has been reduced, so that the conventional vacuum pump can meet the work requirements, so as to ensure the uniformity of film deposition, increase the production capacity of the equipment, and reduce the cost of the equipment (the cost of vacuum and suction filtration is relatively large).
[0021] Each furnace tube 1 has a do...
Embodiment 2
[0026] The difference between this embodiment and Embodiment 1 is that each connecting pipe is provided with an independent angle valve. When only one furnace tube is working, the independent angle valve of the non-working furnace tube can be closed, or when the length of the two furnace tubes At the same time, the pressure in the process chamber of the two furnace tubes can be controlled separately.
[0027] The invention is an atomic layer deposition equipment with multiple furnace tubes. Each furnace tube shares a set of vacuum system, which ensures the uniformity of thin film deposition, improves the total production capacity of the equipment, and reduces the equipment cost required for the same production capacity configuration.
PUM
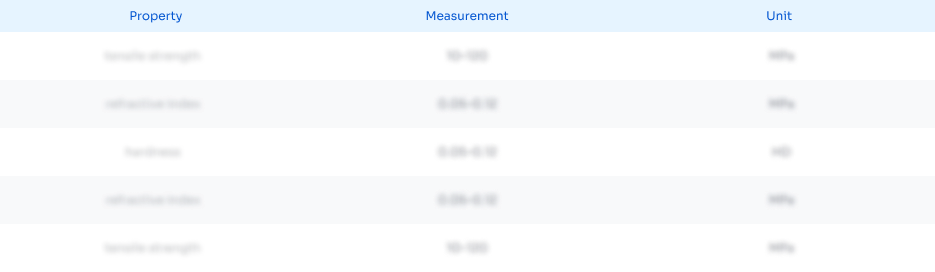
Abstract
Description
Claims
Application Information

- R&D
- Intellectual Property
- Life Sciences
- Materials
- Tech Scout
- Unparalleled Data Quality
- Higher Quality Content
- 60% Fewer Hallucinations
Browse by: Latest US Patents, China's latest patents, Technical Efficacy Thesaurus, Application Domain, Technology Topic, Popular Technical Reports.
© 2025 PatSnap. All rights reserved.Legal|Privacy policy|Modern Slavery Act Transparency Statement|Sitemap|About US| Contact US: help@patsnap.com