Permanent magnet synchronous motor maximum torque current ratio control method based on parameter identification
A technology of maximum torque current, permanent magnet synchronous motor, applied in the direction of single motor speed/torque control, current controller, motor control, etc., can solve the problem of difficult online calculation of MTPA operating point, save debugging time, improve The effect of stability
- Summary
- Abstract
- Description
- Claims
- Application Information
AI Technical Summary
Problems solved by technology
Method used
Image
Examples
Embodiment 1
[0018] A method for controlling the maximum torque-to-current ratio of a permanent magnet synchronous motor based on parameter identification, the control method comprising the following steps:
[0019] Step 1: When the parameters of the motor are nonlinear functions, determine the identification of the flux linkage;
[0020] Step 2: Determine the identification of the derivative of the flux linkage change at the operating point;
[0021] Step 3: Based on the MTPA control rate formed by the derivative of the flux linkage change at the working point in step 2;
[0022] Step 4: Obtain the command value of the current based on the MTPA control rate in step 3.
[0023] Further, the parameters of the motor in step 1 are nonlinear functions, specifically,
[0024] Motor parameter Ψ d , Ψ q for i d i q The nonlinear function of the permanent magnet flux linkage Ψ f It is difficult to accurately identify, so it is not calculated separately to improve the accuracy of the system;...
Embodiment 2
[0083] A 750W permanent magnet synchronous motor was used to carry out related experiments. First, through the actual test, the actual MTPA current curve of the motor was obtained as a comparison; then another set of MTPA current curves was obtained by using the algorithm proposed in this patent. Through comparison, it was found that The proposed algorithm of the present invention is relatively close to the actual MTPA current curve as image 3 shown.
[0084] Figure 4 It is the actual dq-axis current in the no-load state of the motor. It can be seen from the figure that the motor current contains the injected sinusoidal signal of small amplitude.
[0085] Figure 5 is the current dynamic response waveform of the motor, iq changes from 0A to 10A, and then decreases to 0A, and id changes the corresponding current according to the algorithm proposed in this patent.
PUM
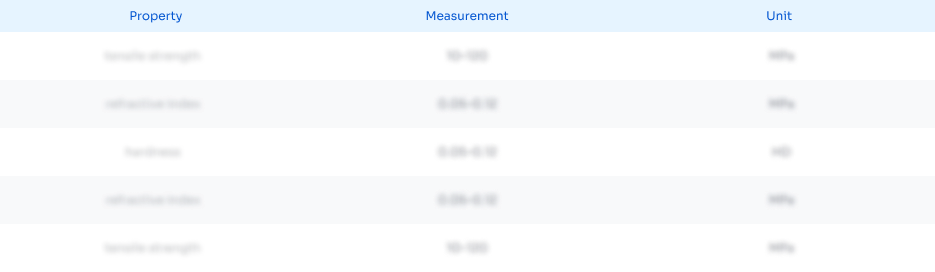
Abstract
Description
Claims
Application Information

- R&D
- Intellectual Property
- Life Sciences
- Materials
- Tech Scout
- Unparalleled Data Quality
- Higher Quality Content
- 60% Fewer Hallucinations
Browse by: Latest US Patents, China's latest patents, Technical Efficacy Thesaurus, Application Domain, Technology Topic, Popular Technical Reports.
© 2025 PatSnap. All rights reserved.Legal|Privacy policy|Modern Slavery Act Transparency Statement|Sitemap|About US| Contact US: help@patsnap.com